CFD-DEM coupling model of a transfer chute for dust control
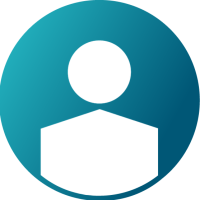

A transfer chute is a critical component in material handling systems, commonly found in mining industries. It is essentially a passage through which bulk materials are transferred from one conveyor to the other.
In these systems, dust is an unwanted byproduct, and its generation can not only cause operational inefficiencies, but also pose health hazards to workers. To mitigate this, modelling a transfer chute using a coupled CFD-DEM model can help derive crucial insights into the system behavior.
Altair provides solutions to model these using a very high-fidelity DEM tool called EDEM, coupled with a general purpose CFD solver called AcuSolve.
The CAD and simulation files (both EDEM and AcuSolve/Simlab) can be found in the attachments.
The key steps to setup a CFD-DEM model of a transfer chute are:
Step 1: Setup the EDEM model
You can find the setting up of the EDEM model here: EDEM Tutorial: Rock Box
Step 2: Clean the geometry within SimLab (pre-processing tool for the coupled simulation)
CFD generally requires volumes to do its analysis on, so please make sure to fill the chute to make it a volume instead of a hollow part. You can do so, using the 'Fill Hole' feature in SimLab.
The airflow over the conveyors is generally not important for dust generation/control simulations, unless the conveyors are covered. If you are interested in modelling the air flow over the conveyors, please make sure to close the conveyor and use the volume to model within CFD.
Once the volumes are prepared, mesh the CFD volume.
The open faces of the chute have 'Outlet' boundary conditions (orange). The faces attached to a conveyor or any moving part will have a 'Wall' boundary condition with the appropriate velocity to it (brown). All other faces of the chute will have Default Wall Boundary conditions.
Step 3: Setup the solution within Simlab
The material definition not only contains the fluid and particle definition, but also contains the lift, drag and torque models to be used.
The timestep and the turbulence model also needs to be set in the 'Solution' window.
Make sure to choose the 'h3d' output file format in 'Result Request', so that you can visualize the results within HyperView. From HyperView 2024.0, only h3d results will be read by HyperView, and log files from AcuSolve will not be read.
Step 4: Setup the coupled solution within Simlab
Once the solutions are prepared, setup a coupled simulation for a 'Flow+EDEM' solution. Run the simulation from Simlab after the coupling server is started within EDEM.
Step 5: Visualize the results within HyperView
Load the .dem file (for EDEM) within HyperView. Once it is loaded, load the h3d file (for AcuSolve) after selecting the 'Overlay' button. This will ensure that both results are overlaid on each other, and you can visualize both EDEM and AcuSolve results together.
A CFD-DEM coupled simulation like the above can help assess the dust generation within the system.
Critical parameters like the volumetric air flow rate through the chute and the pressure at specific locations, can be calculated. These can be used to alter the chute design or the operational parameters to reduce the amount of dust generated. Key things to reduce the dust would be to reduce the angle of impact of the material to the belt, and also making sure that fluid is not trapped within the bulk material, which after impact, may try to escape eventually leading to dust generation
Please refer to these webinars for details on how to reduce dust for a transfer chute:
settling-the-dust-how-to-reduce-using-simulation-design
using-particle-fluid-simulation-to-control-dust-in-conveyor-transfer-chutes
How to optimise transfer chute design
If you are interested in learning more about how to optimise the design of a transfer chute, you can find more information here: How to optimise Transfer Chutes design with the Discrete Element Method (DEM).