Simulating a 3D Printed ABS component.
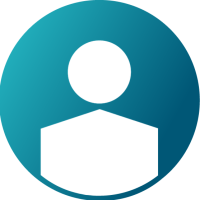

I'm trying to carry out Linear static analysis of my 3D printed(FDM) component which is made up of Acrylonitrile butadiene styrene Plastic (ABSplus P430). Assuming that ABS is relatively Isotropic, i've carried out my analysis using the basic Isotropic - MAT1 card. But in reality, ABS shows anisotropy. I wanted to Simulate it as an Anisotropic Material in HyperWorks. What all parameters & testing data would be required for that? Also, is it right to carry out a linear static analysis of a Plastic material or do i need to do something else. I could find much relevant data regarding this topic.
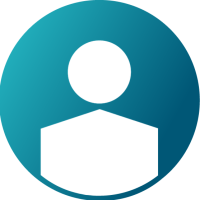

Hi VIshal,
Depends on what type of simulation.
If it is say three point bending simulation then you can refer to ASTM standard guidelines.
Hi Prakash, Thanks for the response.
My Component is an Arm, Fixed at one end & Loaded on the other. Assuming that i just need to carry out basic FEA of the arm( say Linear Static) considering the Anisotropy of the material, how do i achieve it? I couldn't find relevant tutorials regarding it. Basically, FEA of a Plastic component.
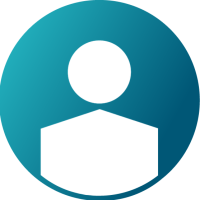

Hi Vishal,
You can MAT2 card to enter anisotropic material properties for 2D elements.
Or,
Approximating to Orthotropy, you can use MAT8 card (for 2D elements), MAT9, MAT9ORT (3D elements)
Hi VIshal,
Depends on what type of simulation.
If it is say three point bending simulation then you can refer to ASTM standard guidelines.