How to synchronise my ADC with PWM anyone please help
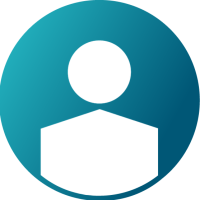

Submitted by Aditya23456 on Sun, 04/07/2013 - 05:38
My main project is having maximum power point tracking of a pv cell using dspa kit...For this process I need my DSPA kit to sense V and I as input and calculate power(ie V*I) and it needs to compare its new power with power old and thereby varies its duty cycle in such a way that power stays outputs constant power and maximuk power too...I m using VISSIM software for this..I m trying to sense V and I through input ports of my DSPA kit by ADC functioning but I m not understanding how to link this output to ePWM in such a way that it varies duty cycle dynamically..Tutorials given are more of complex kind and they r trying to explain cases with 2 or more PWM units which is not needed in my case..ANyone plzz help because my project submission date is coming soona nd I m done with my hardware part ie boost converter , driver circuit etc etc..I hope I m clear if I not..I m ready to type it even more profoundly.
Thanking you, Aditya