3-point Bending of Carbon Fibre Sandwhich Panel
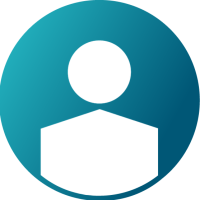

Hi,
Answers
-
Hi,
1. PCOMPP defines the properties of a composite laminate (2D) material used in ply-based composite definition. PSOLID defines the properties of solid elements, referenced by CHEXA, CPENTA, CPYRA and CTETRA elements. For other properties refer to Optistruct help.
2.PCOMPP or PSHELL property is used on the skin, while PSOLID is used for the core.
3. MAT8 will have a bending stiffness
4. MAT9 is compatible with PSOLID
5. Use PSOLID for solid element honeycomb material
If the anticipated deflection is large the explicit time integration scheme (RADIOSS) could be more computationally efficient.
There are a couple of tutorials about three-point bending: RD-T: 3060 Three Point Bending & RD-T: 3595 Three Point Bending with HyperMesh.
There was recently a similar thread:
https://community.altair.com/community?id=community_question&sys_id=3096407a1b2bd0908017dc61ec4bcb5fPlease do not open multiple threads with the same content, because this clutters the forum.
Regards
0 -
Hi,
Sorry that I have only just seen your reply and thank you very much for your response. I was waiting to receive a notification email because I selected that option on the site but never got one unfortunately.
1. You mention that MAT8 has bending stiffness so I checked the MAT8 property card again and saw that the only properties required that are out of plane are G1Z and G2Z, these are not bending stiffness values so do you mean it works it out based on the card inputs (E1, E2, NU12, G12, G1Z, G2Z, A1, A2)?
2. You also mention that 'PCOMPP or PSHELL property is used on the skin.' Are there any particular reasons for selecting one over the other?
3. You mention the use of the 'explicit time integration scheme (RADIOSS)', I am completely new to the software but from my understanding from looking up what this means I have seen an explanation which says: 'the explicit scheme determines the velocities and displacements by direct integration of nodal accelerations.' Does this also then provide the force (load) of the cylinderical 3-point bending load applicator? So would it be possible to output a load-displacement graph typical of a 3-point bending test with this method?
4. Also if this method is rather complicated are there any simple ways of just applying several different load values and then simulating the deflection of each defined load? (The point of this for me would be to workout the flexural rigidity from several load-displacement values from the software.)
Regards
0 -
No problem, glad to help.
1. I haven't yet looked into how bending stiffness is calculated for composites, but from practical experience, the bending stiffness is automatically worked out from those material parameters.
2. PCOMPP is used in ply-based composite while PSHELL is for isotropic 2d elements.
3. Sorry to confuse you with fancy words. Explicit method is used for highly nonlinear problems (geometry, material, contact) like crash, impact and drop test. The answer is yes on both follow-up questions.
Please refer to the already mentioned three-point bending tutorials.
4. You can perform a quasistatic test using an explicit method by slowly ramping up the load and the displacement values can be obtained at each load increment
0 -
Thank you very much for your response.
1. Would PCOMPP be the appropriate option for me because my plan is to define the properties of each ply? (Also the properties aren't isotropic as I have UD layers.)
2. Regarding point 4, you mention doing a quasistatic test....it seems from a quick google that RADIOSS is used to do this? I was wondering if there are any other methods of doing this within altair because chances are I run into a problem and I'm very tight on time at the moment so I'm just trying to keep my options open?
Regards
0 -
1. Yes
2. You can also perform a quasistatic test in Optistruct with NLSTAT analysis (implicit). However, if there are large displacements, rotations or deformations the implicit method could experience convergence difficulties. Also the contact interaction between the supports, impactor and panel could be problematic using implicit method due to sliding contact with friction. This could be simplified by using boundary conditions and loads: trading-off fidelity for computational efficiency.
0 -
Thank you for your response. Unfortunately I'm getting a license error when opening the software. The altair_lic.dat file can't be found but I have it copied in to the security folder and followed all the instructions from the license email so it looks like I can't use the software. I spent all day trying to sort this out changing file directory permissions etc. I may have to change to ANSYS.
0 -
Hopefully, you'll be able to resolve the licensing issue.
If you decide to use Optistruct observe how 3-point bend example is set up: OS-E: 0180 3-Point Bending using RBODY
0