Force calculation issue
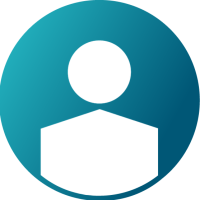
Hi Friends,
I was analyzing a throttle pedal where I experienced an issue of force even though it was not too complex. I was trying to obtain force acting in pedal due to a rotational displacement provided in the hinge joint due to spring force. I initially did a mistake on constraints and now resolved which was there was 12DOF extra due to presence of 2 additional unconstrained member but even after I constrained also the spring force showed up to around 80N but the value of pedal force was 0.0009N maximum. Which seems to be lesser can anyone help me out of this issue.
Thank you
Best Answer
-
"But if theses redundancies are removed we get the perfect force acting in systems."
This only applies if you do one (or both) of the following:
1. Use bushings (or compliant joints) instead of non-compliant joints
2. Replace bodies with flexbodies.
If the model is overconstrained, and motionsolve removes constraints, you do not get forces in the removed DOF.
If you "fix" the overconstraints by changing the joint type (say from a revolute joint to a ball joint), you have the same issue as if motionsolve removed the constraints automatically.....you won't get moments if you are using a ball joint that you would otherwise get by using a revolute joint.
1
Answers
-
Without being able to look at the model, it's going to be difficult to provide specific advice.
1. Look at your .log file, make sure there are no redundant constraint messages. If there are, you need to fix those first.
2. If your simulation is running as a kinematic analysis (again, check the .log file) then the forces may not calculated as you would expect.
3. Pay attention to how you are creating your outputs. The model may be correct, but you have not defined your outputs correctly, or are not plotting the results correctly.
1 -
Thank you Chris for your answer.
1. I have checked the .log file for reduntancy and also DOF calculation it is showing zero. Thus there is no reduntancy.
2. As you have mentioned to check on the .log for kinematic analysis it is running on kinematic analysis. Hence how can we get the correct results. ( For example when the stiffness is changed the pedal force should change but here in my case the stiffness variation doesnt affect any of the force values. As I have mentioned earlier the force value itself is so low.)
3. I have tried about three ways to find the output one way with expression, the other way by force on joint and then force on bodies. The last two gives the same results but for the first the value comes out to be zero.
The model I have obtained from grab cad which I am attaching here.
@Chris Coker I further request for your help to resolve this issue.
Thank you in advance
0 -
Kiran Govind said:
Thank you Chris for your answer.
1. I have checked the .log file for reduntancy and also DOF calculation it is showing zero. Thus there is no reduntancy.
2. As you have mentioned to check on the .log for kinematic analysis it is running on kinematic analysis. Hence how can we get the correct results. ( For example when the stiffness is changed the pedal force should change but here in my case the stiffness variation doesnt affect any of the force values. As I have mentioned earlier the force value itself is so low.)
3. I have tried about three ways to find the output one way with expression, the other way by force on joint and then force on bodies. The last two gives the same results but for the first the value comes out to be zero.
The model I have obtained from grab cad which I am attaching here.
@Chris Coker I further request for your help to resolve this issue.
Thank you in advance
If you are running a kinematic analysis, you are no longer solving for F=m*a
A zero DOF model is a kinematic analysis.
You need to increase the DOF of your model. You can do this one of two ways
1) Change one or more more joints from non-compliant to compliant
2) Chane one or more bodies to flexbodies.
0 -
Chris Coker_21312 said:
If you are running a kinematic analysis, you are no longer solving for F=m*a
A zero DOF model is a kinematic analysis.
You need to increase the DOF of your model. You can do this one of two ways
1) Change one or more more joints from non-compliant to compliant
2) Chane one or more bodies to flexbodies.
Ok,
So it means that I have to give the forces as well as increase the DOF for dynamic analysis.
I was first going through the rigid body systems as a whole. So from this regard I have to make the system dynamic by increasing the DOF by making adjustments in joints with all the necessary force acting on joints. Is that a correct interpretation of what you have said?
Thank you
0 -
Kiran Govind said:
Thank you Chris for your answer.
1. I have checked the .log file for reduntancy and also DOF calculation it is showing zero. Thus there is no reduntancy.
2. As you have mentioned to check on the .log for kinematic analysis it is running on kinematic analysis. Hence how can we get the correct results. ( For example when the stiffness is changed the pedal force should change but here in my case the stiffness variation doesnt affect any of the force values. As I have mentioned earlier the force value itself is so low.)
3. I have tried about three ways to find the output one way with expression, the other way by force on joint and then force on bodies. The last two gives the same results but for the first the value comes out to be zero.
The model I have obtained from grab cad which I am attaching here.
@Chris Coker I further request for your help to resolve this issue.
Thank you in advance
This is CAD data, not a model. Unfortunately I do not have the time to recreate a model for you from scratch. If you are able to supply the .mdl file you are a working with, then someone on the forum here can assist you better.
0 -
Chris Coker_21312 said:
This is CAD data, not a model. Unfortunately I do not have the time to recreate a model for you from scratch. If you are able to supply the .mdl file you are a working with, then someone on the forum here can assist you better.
Along with the force applied I should have more DOF is that correct?
I am really sorry for providing the wrong file I am uploading the .mdl file.
Thank you for your time.
0 -
Kiran Govind said:
Along with the force applied I should have more DOF is that correct?
I am really sorry for providing the wrong file I am uploading the .mdl file.
Thank you for your time.
You also need to provide the .h3d file that the .mdl file is referencing.
Helpful hint: You can use File -> Export -> Model -> Export model, and you can use that to create an archive that contains all of the data referenced by that model.
0 -
Chris Coker_21312 said:
You also need to provide the .h3d file that the .mdl file is referencing.
Helpful hint: You can use File -> Export -> Model -> Export model, and you can use that to create an archive that contains all of the data referenced by that model.
Sorry for these inconvenience I am uploading all those related files of model.
I suppose I have included all the files.
Kindly please help for these two doubts:
1) Is this the same reason of kinematic analysis that varying the spring constant doesnt affect the force
2) Even after I change to dynamic analysis with the angular motion with extended DOF eventhough value of compliant has been given arbitrarily the value of forces in pedal doesnt show up.
3) Kindly if you could verify if I have done is correct or give me some suggestion of altering those it would be most helpful.
I am attaching the dynamic mode analysis as next reply message the value given to one compliantt joint is arbitrary.
Thank you
0 -
Kiran Govind said:
Sorry for these inconvenience I am uploading all those related files of model.
I suppose I have included all the files.
Kindly please help for these two doubts:
1) Is this the same reason of kinematic analysis that varying the spring constant doesnt affect the force
2) Even after I change to dynamic analysis with the angular motion with extended DOF eventhough value of compliant has been given arbitrarily the value of forces in pedal doesnt show up.
3) Kindly if you could verify if I have done is correct or give me some suggestion of altering those it would be most helpful.
I am attaching the dynamic mode analysis as next reply message the value given to one compliantt joint is arbitrary.
Thank you
These are the dynamic analysis model and and h3d file.
0 -
Kiran Govind said:
These are the dynamic analysis model and and h3d file.
You need to provide the file: Throttle pedal assembly Rev 01_graphic.h3d
which is referenced by the .mdl file
Helpful hint: You can use File -> Export -> Model -> Export model, and you can use that to create an archive that contains all of the data referenced by that model.
0 -
Chris Coker_21312 said:
You need to provide the file: Throttle pedal assembly Rev 01_graphic.h3d
which is referenced by the .mdl file
Helpful hint: You can use File -> Export -> Model -> Export model, and you can use that to create an archive that contains all of the data referenced by that model.
This is kinematic analysis
0 -
Kiran Govind said:
This is kinematic analysis
For dynamic
0 -
Ok, there's a number of things going on here.
1) The model is a lot more complex that it needs to be. You can use "Merge Bodies" to combine bodies rather than spend time connecting them via fixed joints
2) If you have a simple model like this (0 DOF), you are not going to get the forces at that joint. This is a situation where the model may seem very simple, but the way to get the correct result out is somewhat complicated due to the nature of the model. If you were just interested in the force in the spring, this would be trivial.
3) A somewhat complicated way to solve this problem, is turn the revolute joint to a compliant joint (thus making it non-kinematic), and then use Marker Motion to apply the motion, and then get output the force between the two markers. I would recommend working through some of our MotionView tutorials, starting with MV-100.
Now, in the time it took me to write this reply, I rebuilt the entire model using Inspire Motion, and plotted the torque curve. By default the joints are compliant, and a Motor Controller is used to create a torque to turn the joint using the desired rotation curve.
Anytime you have really complete CAD data (like this example), you should consider Inspire Motion as your first choice. If needed, you can always export the .mdl file to MotionView.
1 -
Chris Coker_21312 said:
Ok, there's a number of things going on here.
1) The model is a lot more complex that it needs to be. You can use "Merge Bodies" to combine bodies rather than spend time connecting them via fixed joints
2) If you have a simple model like this (0 DOF), you are not going to get the forces at that joint. This is a situation where the model may seem very simple, but the way to get the correct result out is somewhat complicated due to the nature of the model. If you were just interested in the force in the spring, this would be trivial.
3) A somewhat complicated way to solve this problem, is turn the revolute joint to a compliant joint (thus making it non-kinematic), and then use Marker Motion to apply the motion, and then get output the force between the two markers. I would recommend working through some of our MotionView tutorials, starting with MV-100.
Now, in the time it took me to write this reply, I rebuilt the entire model using Inspire Motion, and plotted the torque curve. By default the joints are compliant, and a Motor Controller is used to create a torque to turn the joint using the desired rotation curve.
Anytime you have really complete CAD data (like this example), you should consider Inspire Motion as your first choice. If needed, you can always export the .mdl file to MotionView.
First of all thank you for your valuable time.
I understood what the complexity is about getting the results by markers and getting the force from it.
I will perform the analysis based on your suggestion of merging and compliant one and thus dynamic one and get it by the marker method.
Thank you
0 -
Chris Coker_21312 said:
Ok, there's a number of things going on here.
1) The model is a lot more complex that it needs to be. You can use "Merge Bodies" to combine bodies rather than spend time connecting them via fixed joints
2) If you have a simple model like this (0 DOF), you are not going to get the forces at that joint. This is a situation where the model may seem very simple, but the way to get the correct result out is somewhat complicated due to the nature of the model. If you were just interested in the force in the spring, this would be trivial.
3) A somewhat complicated way to solve this problem, is turn the revolute joint to a compliant joint (thus making it non-kinematic), and then use Marker Motion to apply the motion, and then get output the force between the two markers. I would recommend working through some of our MotionView tutorials, starting with MV-100.
Now, in the time it took me to write this reply, I rebuilt the entire model using Inspire Motion, and plotted the torque curve. By default the joints are compliant, and a Motor Controller is used to create a torque to turn the joint using the desired rotation curve.
Anytime you have really complete CAD data (like this example), you should consider Inspire Motion as your first choice. If needed, you can always export the .mdl file to MotionView.
Here I am planning to obtain the pedal force due to the motion given in the hinge from the effect of springs so I think the method of markers will provide the required results.
0 -
Chris Coker_21312 said:
Ok, there's a number of things going on here.
1) The model is a lot more complex that it needs to be. You can use "Merge Bodies" to combine bodies rather than spend time connecting them via fixed joints
2) If you have a simple model like this (0 DOF), you are not going to get the forces at that joint. This is a situation where the model may seem very simple, but the way to get the correct result out is somewhat complicated due to the nature of the model. If you were just interested in the force in the spring, this would be trivial.
3) A somewhat complicated way to solve this problem, is turn the revolute joint to a compliant joint (thus making it non-kinematic), and then use Marker Motion to apply the motion, and then get output the force between the two markers. I would recommend working through some of our MotionView tutorials, starting with MV-100.
Now, in the time it took me to write this reply, I rebuilt the entire model using Inspire Motion, and plotted the torque curve. By default the joints are compliant, and a Motor Controller is used to create a torque to turn the joint using the desired rotation curve.
Anytime you have really complete CAD data (like this example), you should consider Inspire Motion as your first choice. If needed, you can always export the .mdl file to MotionView.
@Chris Coker Just one more doubt based on your answer. The spring force can directly be determined no issue in that. For the pedal force we by using this method of markers we will get the required pedal force right?
Thank you
0 -
I tried by your method just as a trial with arbitrary values was not able to get but have to perform more analysis. @Chris Coker and to anyone who knows here as I have mentioned I am providing the angular displacement of 5 time steps with each steps consisting of each angular displacement. So I would like to know we can obtain the spring force it is easy but I would like to clarify or confirm that it is possible to obtain the pedal force as well right? This is the correct method right? The only issue is with DOF and and the output considerations right?
0 -
Kiran Govind said:
I tried by your method just as a trial with arbitrary values was not able to get but have to perform more analysis. @Chris Coker and to anyone who knows here as I have mentioned I am providing the angular displacement of 5 time steps with each steps consisting of each angular displacement. So I would like to know we can obtain the spring force it is easy but I would like to clarify or confirm that it is possible to obtain the pedal force as well right? This is the correct method right? The only issue is with DOF and and the output considerations right?
Personally, this is not the approach I would use to obtain pedal force. The problem with the current approach is that you are applying an input to the revolute joint. What you will get is the Torque required to move the pedal, which is indirectly related to the pedal force via the moment arm.
Rather than apply a torque to the joint, if I want to know the force at the pedal, I need to apply a force at the pedal, or apply a displacement (usually in the form of an actuator of some sort). The force can be a function of time, and I can also measure the displacement.
I've attached a simple example of how to do this using an applied force at the pedal.
1 -
Chris Coker_21312 said:
Personally, this is not the approach I would use to obtain pedal force. The problem with the current approach is that you are applying an input to the revolute joint. What you will get is the Torque required to move the pedal, which is indirectly related to the pedal force via the moment arm.
Rather than apply a torque to the joint, if I want to know the force at the pedal, I need to apply a force at the pedal, or apply a displacement (usually in the form of an actuator of some sort). The force can be a function of time, and I can also measure the displacement.
I've attached a simple example of how to do this using an applied force at the pedal.
Ok. I tried to open the file it opens with some errors and quasi-static analysis is failing I will attach the .xml file.
I suppose you have used quasi static since the forcing is time dependent
But here the force is given and the displacement and spring force is found right with time dependent forcing.
So for obtaining pedal force with displacement three methods can be done
1) by applying moment in hinge.
2) Forcing time dependent
3) Actuator displacement
In first it gets directly pedal force
In second the displacement is obtained
In third pedal force can be obtained
Thank you
0 -
Kiran Govind said:
Ok. I tried to open the file it opens with some errors and quasi-static analysis is failing I will attach the .xml file.
I suppose you have used quasi static since the forcing is time dependent
But here the force is given and the displacement and spring force is found right with time dependent forcing.
So for obtaining pedal force with displacement three methods can be done
1) by applying moment in hinge.
2) Forcing time dependent
3) Actuator displacement
In first it gets directly pedal force
In second the displacement is obtained
In third pedal force can be obtained
Thank you
How can a displacement be applied in pedal with actuator.
0 -
Kiran Govind said:
How can a displacement be applied in pedal with actuator.
Please find attached a sample model that shows how to model an actuator. You can use this as an example for how to implement something similar for your application.
If these responses have been helpful, it will be useful to other if you are mark replies as "helpful" so others can learn as well.
1 -
Chris Coker_21312 said:
Please find attached a sample model that shows how to model an actuator. You can use this as an example for how to implement something similar for your application.
If these responses have been helpful, it will be useful to other if you are mark replies as "helpful" so others can learn as well.
Sure the whole was helpful. I thought to mention at the end.
thank you and I will try and contact if there is any issue
Thank you
0 -
Meanwhile I was asking these querries I was trying the flex body analysis. I was able to analyse for a model of sla of thhe altair model. But I was just trying too analysis for the connecting rod of 4bar mechanism. I got an error while doing the flex prep pasting the error here. Can you or anyone clarify this error.
" *** See next message about line 253 from file:
C:/Users/kiran/Downloads/four-bar-mechanism-11.snapshot.11/Connecting rod FEM_prp.fem
"CTRIA3 20 0 110 39 109"
This line was interpreted as:
253:CTRIA3, 20, 0, 110, 39, 109"The analysis with actuator seems more good and planning for the moment method.
Please clarify the reason for the above mentioned error.
0 -
Kiran Govind said:
Meanwhile I was asking these querries I was trying the flex body analysis. I was able to analyse for a model of sla of thhe altair model. But I was just trying too analysis for the connecting rod of 4bar mechanism. I got an error while doing the flex prep pasting the error here. Can you or anyone clarify this error.
" *** See next message about line 253 from file:
C:/Users/kiran/Downloads/four-bar-mechanism-11.snapshot.11/Connecting rod FEM_prp.fem
"CTRIA3 20 0 110 39 109"
This line was interpreted as:
253:CTRIA3, 20, 0, 110, 39, 109"The analysis with actuator seems more good and planning for the moment method.
Please clarify the reason for the above mentioned error.
The message you are getting is coming from OptiStruct. You should post a separate question about this in the OS forum
0 -
@Chris Coker in this analysis of JCB back hoe I tried of analysis with DoF =0 and it give the motion but force calculation eventhough I havnt increased the DOF. The software is itself changing why is it causing and is it the reason why torque values obtained by using MOTION expression so high. I am attaching the screenshot for those.
Similar case I experiensed for the throttle pedal where this torque value by MOTION expression or T Expression is either so much high or zero why is it causing even when it is at DOF>0 also and even at DOF=0 it starts the error message as reducing rreduntancy.
Please help me out.
Thank you
0 -
Model is overconstrained. If the model is overconstrained, motionsolve will remove constraints until it can reach a solvable model. Where a constraint is removed, by definitions there will be no forces transmitted in that direction. Therefore the forces throughout the model may not be physically realistic.
Fix the overconstraints by using bushings, or flexible bodies. You may also need to change joint types. Do you need a revolute joint at each end of the actuator, when in reality a ball joint at one end and a u-joint at the other end would have less constraints. However if your need moments into those joints, then of course a ball joint will not work.
The best suggestion here would be to start with a simple model, and work out the details of that first, and then add complexity. "Crawl, walk, run"
0 -
Chris Coker_21312 said:
Model is overconstrained. If the model is overconstrained, motionsolve will remove constraints until it can reach a solvable model. Where a constraint is removed, by definitions there will be no forces transmitted in that direction. Therefore the forces throughout the model may not be physically realistic.
Fix the overconstraints by using bushings, or flexible bodies. You may also need to change joint types. Do you need a revolute joint at each end of the actuator, when in reality a ball joint at one end and a u-joint at the other end would have less constraints. However if your need moments into those joints, then of course a ball joint will not work.
The best suggestion here would be to start with a simple model, and work out the details of that first, and then add complexity. "Crawl, walk, run"
Yes of course, I was did with those basic models and in those cases when considering forces there was not much difficulties. But here only these issues came of over constrained. I took the revolute since it would be easier to calculate moment else it cant be find. So I should change either to flexible or to bushings or even should not consider the forcing in all joints rather convert to other joints and proceed.
0 -
Chris Coker_21312 said:
Model is overconstrained. If the model is overconstrained, motionsolve will remove constraints until it can reach a solvable model. Where a constraint is removed, by definitions there will be no forces transmitted in that direction. Therefore the forces throughout the model may not be physically realistic.
Fix the overconstraints by using bushings, or flexible bodies. You may also need to change joint types. Do you need a revolute joint at each end of the actuator, when in reality a ball joint at one end and a u-joint at the other end would have less constraints. However if your need moments into those joints, then of course a ball joint will not work.
The best suggestion here would be to start with a simple model, and work out the details of that first, and then add complexity. "Crawl, walk, run"
@Chris Coker I did by your suggestion about minimizing the constraints by utilizing other type of joints and maintaining the motion. I could do it till DOF=0 and for DoF>0 I have to make it compliant or flex body which I havn't started yet. Since in the real JCB case the cylindrical link will connect to the secondary arm directly thus reducing one input but here it is not possible since we have to give motion in revolute as there is no connection.
From maintaining DoF = 0 I initially calculated moment in revolute but that was my computational mistake and thus changed to force in translational joint of cylinder and obtained out to be one link of 14KN and other about 140N.
I have a small doubt will the change of joints affects the result of force. and also if the software itself reduces redundancy there are chances of false results in some cases. right??
Please provide your reply and feedback on all these notes.
Thank you
0 -
"I have a small doubt will the change of joints affects the result of force. and also if the software itself reduces redundancy there are chances of false results in some cases. right??"
This is exactly the point I have been trying to make. If redundant constraints are removed that affect the loads in the system, the loads will be "false" as you say, although the kinematics (the motion of the mechanism) will be correct.
0 -
Chris Coker_21312 said:
"I have a small doubt will the change of joints affects the result of force. and also if the software itself reduces redundancy there are chances of false results in some cases. right??"
This is exactly the point I have been trying to make. If redundant constraints are removed that affect the loads in the system, the loads will be "false" as you say, although the kinematics (the motion of the mechanism) will be correct.
Ok now with these analysis I understood. Even though the motion is perfect in some of the analysis this reduction in joints by software is giving some force which are not at all related to the analysis in some cases but in some others it is giving the correct forces. But if theses redundancies are removed we get the perfect force acting in systems.
I additionally wanted to know suppose if a system is being analysed with a revolute joint and connected link s having a revolute joint but it is not a case of redundancy will the change of joint from spherical affect the results? or when will it affect other than in the case of redundancy.
Sorry for taking you time. But these are the doubts came into my mind.
Thank you
0