Complex "Unconventional" composite meshing
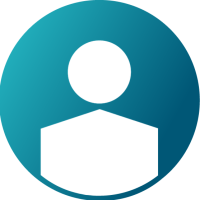
Hi all,
I've got myself into a bit of a problem meshing a 'composite' part.
I'm investigating the use of continuous fiber reinforced 3D printing as part of a project at Uni, where I'm using the Markforged 3D printer to specify fiber orientation etc for max stiffness/minimum weight. I have successfully simulated my basic tensile tests in ABAQUS but I'm now looking to use OptiStruct to optimise the lay-up of my design, which is a printed joint connecting two tubes at 90-deg angle with a flanged base for mounting.
The design is unconventional for composites, ie not a thin shell where 2D elements can be used. I've done a few of the Hyperworks composites tutorials but none are representative of my problem so I'm looking for guidance on the meshing of the part.
Being 3D printed, it is manufactured layer by layer, meaning the fibers are all parallel to the base plane, but the part has a complex geometry with different wall thicknesses, tapers etc.
I reviewed using midsurfaces but I couldn't make any real progress with it. I know you can use the MAT9 for 3D composites but will this still enable me to optimise the laminate layups? I was maybe thinking of breaking down my model into each part i.e. base, stiffener and joint?
I'm looking forward to hearing what people say - I'm fairly new to Hyperworks but I'm really enjoying learning it!!
Answers
-
I stiill haven’t managed to get anywhere with this. Does anyone have any suggestions please?
0 -
Hi,
Please find attached the document on optimization of composites for your reference.
Thank you.
0