Getting Twist Angle on Shaft Under Torsion
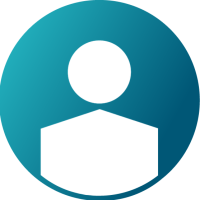
Hi Everyone,
I'm running a simulation where the model is a shaft under pure torsion loading. My goal is just to validate the result of my FEA and see if it matches my calculation. I'm using a tetramesh model and even thoughthe meshing is coarse I kind of get similar value to my hand calculation on the shear stress part.
The problem comes when I tried to generate the twist angle of the shaft, for some reason the value for that is really small compared to my calculation. Does anyone experience this? What do I need to do to fix this?
Attached is the file that I'm using.
Best,
Ariq
Answers
-
Hi
Based on the geometry (D=3.84, and length=18)
, the material (Poison=0.3 and Young Modulus = 1,060,000)
and load (torque = 1,000) the value of angle is estimated as:
Angle is about 0.002rad
Is this the estimated value you are getting?
Regards
0 -
Rogerio Nakano_21179 said:
Hi
Based on the geometry (D=3.84, and length=18)
, the material (Poison=0.3 and Young Modulus = 1,060,000)
and load (torque = 1,000) the value of angle is estimated as:
Angle is about 0.002rad
Is this the estimated value you are getting?
Regards
Yes. Unfortunately in my model it did not generate any twist angle. It says 0 for it. Do you know what might have happened?
0 -
Achmad Zufar said:
Yes. Unfortunately in my model it did not generate any twist angle. It says 0 for it. Do you know what might have happened?
Hi
if you need the angle of shaft twist , what you could do is
- in HyperView create a local cylindrical coordinate system that is centered in the face that you are applying torque, with the z-axis aligned to the shaft axis.
- So that x -> radial disp (r) and y-> angular disp (theta)
- when contouring, you select the displacement result, y-component. Also select the user defined coordinate system and contour.
- That will contour the angular displacement of the nodes relative to the local cylindrical coordinate system
- you can query the external diameter nodes and check the rotation of this nodes, relative to the origin of local coordinate system, that is the center of rotation you selected.
I hope that is helpful
Regards
0