Too slow RCS Analysis when materials applied
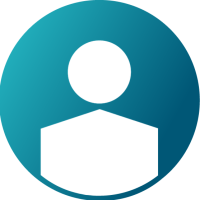
I'm using Altair FEKO software to analyze RCS of certain model. especially what I'm now doing is applying materials on surface of model and gaining RCS result with PO solver.
But here is the thing: when FEKO in my computer claculates RCS when default PEC applied, the calculation speed is acceptable, for 15m aircraft CAD model, Caculation finished within a week, but once I apply Aluminum material and run with same parameter, the calculation speed significantly gets slow.
I just estimated how long it will take with aluminum coated, and it was at least a month to finish calculation of RCS with 0~180 degree theta(elevation) and 0~360 degree phi(azimuth).
I think I did everything correct before I hit run FEKO button to start RCS calcuration, but there is a possibility that I made wrong for some part, so I attach images files in order of how I did, and also a .cfx file.
FYI my computer hardware is
CPU: AMD Ryzen Threadripper 2950x (16 core 32 thread)
RAM: 128G GDDR4
storage: enough capacity and nvme SSD
GPU: GTX1060 6G
0. the main purpose of using FEKO: Calcuration of RCS of aircrafts, and for now real size UAV CAD file is used. I want to know how RCS gained if aluminum coating is applied on model. with PO solver, X band 8GHz, FarField, RCS of particular elevation and azimuth angles.
1. Import geometry model: mainly step file
2. Set frequency: 8GHz
3. Set plane wave source: 0~180 degree for theta and phi
4. Set Farfield request: I want to know monostatic RCS so 'plane wave incident direction' chosen
5. Making aluminum property under the name of "Aluminum Property". for PO solver when I just select default aluminum medium, FEKO gave me "no lossy metalic surface" error so I did this way, manually wirte permittivity and other perperties.
6. Select thickness of Aluminum coating layer, for this case I chose 0.5
7. Change region to free space
8. Applying aluminum layer I created to all faces of CAD model, for this time name of Coating layer is "Aluminum_Layer"
9. Applying PO solver
9. Create mesh. I just use "standard"option for every aircrafts CAD model
and now finally hit Feko Solver to gain RCS of selected CAD model.
I think the problem is related to mesh, but not sure where I was wrong.
I need to know how to solve my time consumption problem in FEKO....
Answers
-
Dear Yun
You mention receiving and error when trying to apply the aluminium as a lossy metallic surface. This is expected as the PO solution does not support such lossy metal surfaces. Your solution of implementing the aluminium as a dielectric coating does not seem valid. Note that with this option you are applying the dielectric as a coating on a PEC face which is not what you require.
Also note that the default model unit is in meters (m). Setting your coating thickness to be 0.5 would therefore result in a 0.5m thick coating.
The PO solver is not well suited to this application as it only considers a single reflection. If multiple reflections (such as interactions between the fuselage and wings) become significant, this solution would not be valid.I would suggest that you consider using the MLFMM solution if you have sufficient resources available. If you do not have sufficient resources to solve this model with the MLFMM, aslo the RL-GO should be considered. Note that both the MLFMM and RL-GO supports the solution of lossy metallic surfaces and both should correctly account for multiple reflections.
I also noticed that you are using a older version of Feko. As the efficiency of the Feko solvers are constantly being improved, it is highly recommended to update to the latest version.Kind regards,
Johan Huysamen
1 -
Johan Huysamen_22531 said:
Dear Yun
You mention receiving and error when trying to apply the aluminium as a lossy metallic surface. This is expected as the PO solution does not support such lossy metal surfaces. Your solution of implementing the aluminium as a dielectric coating does not seem valid. Note that with this option you are applying the dielectric as a coating on a PEC face which is not what you require.
Also note that the default model unit is in meters (m). Setting your coating thickness to be 0.5 would therefore result in a 0.5m thick coating.
The PO solver is not well suited to this application as it only considers a single reflection. If multiple reflections (such as interactions between the fuselage and wings) become significant, this solution would not be valid.I would suggest that you consider using the MLFMM solution if you have sufficient resources available. If you do not have sufficient resources to solve this model with the MLFMM, aslo the RL-GO should be considered. Note that both the MLFMM and RL-GO supports the solution of lossy metallic surfaces and both should correctly account for multiple reflections.
I also noticed that you are using a older version of Feko. As the efficiency of the Feko solvers are constantly being improved, it is highly recommended to update to the latest version.Kind regards,
Johan Huysamen
Thank you for providing me a valuable help about my project, with GO solver I think the calculation speed will be a lot faster than PO. and I have one more question for your reply.
you mentioned that my solution of implementing the aluminum as a dielectirc coating doesn't seem valid, could yo show and teach me how I can apply aluminum material coating on surface of CAD model? I'd would really appreciate it if you provide me a proper way to apply it.
0