Dem-Cfd Modeling of Solid-Fluid Flows
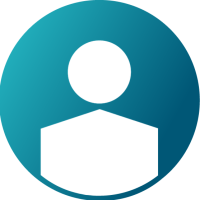
AUTHOR(S)
J. Favier, P. Golz
PUBLISHER
American Institute of Chemical Engineers
SOURCE
The 2006 Spring National Meeting
YEAR
ABSTRACT
Effective modeling of solid-fluid flow requires methods for adequately characterizing the discrete nature of the solid phase and representing the interaction between solids and fluids. CFD multiphase models such as the Euler-Lagrange Method and the Euler-Granular method address the problem within a continuum framework. In continuum models, contact between fluid, particles and boundary surfaces is not considered explicitly with respect to particle inertial and mechanical prop-erties. This can limit the ability of CFD multiphase models to adequately represent particle-particle and fluid-particle interactions and therefore can reduce the accuracy of the prediction of both the fluid and the particle dynamics.This limitation can be overcome by explicit calculation of the particle contact mechanics in a particle-scale reference frame using a Lagrangian approach such as the Discrete Element Method (DEM). Coupling of DEM and CFD provides a means of momentum and energy exchange between solids and fluid, which, in principle, removes the need for some of the semi-empirical approximations employed in CFD solid-fluid models. Coupled DEM-CFD simulation has potentially a very wide range of application and is attracting increasing interest from industry.DEM-CFD models reported in the literature have largely been applied to simulation of fluidised beds and more recently to pneumatic transport of particles. A feature of most of these models is the simple boundary surface geometry and use of mapped, usually Cartesian, meshes. Many industrial processes involved complex geometry, often with moving parts, and complex flow dynamics. Simulation of such systems requires use of unstructured fluid meshes, and the ability to handle energy as well as momentum exchange, turbulent flow, and chemical reactions.This capability is now possible in a commercial environment using co-simulation of EDEM discrete element modeling software with FLUENT. EDEM is an advanced particle mechanics simulation tool employed for modeling of industrial particulate handling and processing operations. It uses a surface mesh to represent boundary surfaces which enables a one-to-one coupling with the boundary surface elements of the CFD fluid volume mesh. EDEM-FLUENT co- simulation is being used to investigate systems such as particle agglomeration and clumping in fluidised beds, dense phase conveying, filtration, solid-liquid mixing, pipe erosion, spray coating and many others. Here we show some applications and assess the opportunities and limitations for application of DEM-CFD simulation of industrial solid-fluid system.
KEYWORDS
applications, CFD, coupling, EDEM, FLUENT, multi-phase