A DEM study of powder spreading in additive layer manufacturing
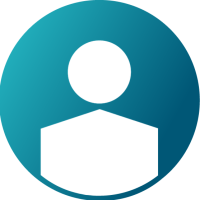
AUTHOR(S)
A. E. Bayly, Y.M. Fouda
PUBLISHER
Springer
SOURCE
Granular Matter
YEAR
ABSTRACT
In this paper, discrete element method simulations were used to study the spreading of an idealised, blade based, powder coating system representative of the spreading of spherical, mono-sized, non-cohesive titanium alloy (Ti6AlV4) particles in additive layer manufacturing applications. A vertical spreader blade was used to accelerate a powder heap across a horizontal surface, with a thin gap between the blade and the surface, resulting in the deposition of a thin powder layer. The results showed that it is inevitable to deposit a powder layer with a lower packing fraction than the initial powder heap due to three mechanisms: shear-induced dilation during the initiation of powder motion by the spreader; dilation and rearrangement due to powder motion through the gap; and the inertia of the particles in the deposited powder layer. It was shown that the process conditions control the contribution of these three mechanisms, and that the velocity profile in the shear layer in front of the gap is critical to the final deposited layer packing fraction. The higher the mean normalised velocity in the shear layer the lower the deposited layer packing fraction. The gap thickness and the spreader blade velocity affect the properties of the deposited layer; with the former increasing its packing fraction and the latter decreasing it. The analysis presented in this study could be adapted to powders of different materials, morphologies and surface properties.
KEYWORDS
Additive manufacturing (AM), Dilation, Discrete Element Method (DEM), Metal powders, powder bed fusion, Powder spreading