Numerical Modeling for Simulation of Compaction of Refractory Materials for Secondary Steelmaking
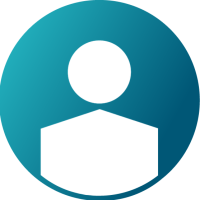
AUTHOR(S)
A. González Marcos, C. Ramirez-Aragon, F. Alba-Elías, J. Ordieres-Mere
PUBLISHER
MDPI
SOURCE
Materials 2020
YEAR
ABSTRACT
The purpose of this work is to simulate the powder compaction of refractory materials, using the discrete element method (DEM). The capability of two cohesive contact models, implemented in dierent DEM packages, to simulate the compaction of a mixture of two refractory materials (dead burnt magnesia (MgO) and calcined alumina (Al2O3)) was analyzed, and the simulation results were compared with experimental data. The maximum force applied by the punch and the porosity and final shape quality of the compact were examined. As a starting point, the influence of Young’s modulus (E), the cohesion energy density (CED), and the diameter of the Al2O3 particles (D) on the results was analyzed. This analysis allowed to distinguish that E and CED were the most influential factors. Therefore, a more extensive examination of these two factors was performed afterward, using a fixed value of D. The analysis of the combined eect of these factors made it possible to calibrate the DEM models, and consequently, after this calibration, the compacts had an adequate final shape quality and the maximum force applied in the simulations matched with the experimental one. However, the porosity of the simulated compacts was higher than that of the real ones. To reduce the porosity of the compacts, lower values of D were also modeled. Consequently, the relative deviation of the porosity was reduced from 40–50% to 20%, using a value of D equal to 0.15 mm.
KEYWORDS
cohesive contact models, Discrete Element Method (DEM), Experiments, Powder Compaction, refractory materials