Numerical research on wear characteristics of drum based on discrete element method (DEM)
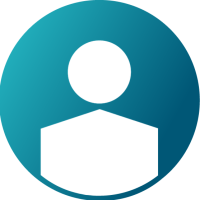
AUTHOR(S)
L. Zhao, X. Jin, X. Liu
PUBLISHER
Elsevier
SOURCE
Engineering Failure Analysis
YEAR
ABSTRACT
Drum works on high impact and non-linear load condition, which easily results in severe wear and failure. However, the wear mechanism and how factors influence the wear characteristics of the spiral drum are still not clear until now. Thus, combining the physical and mechanical properties experiment results of coal samples, the coupling model of the drum cutting in complex coal seam was established using discrete element method. Then, the interaction force between drum and particles, the wear distribution characteristics of drum were all studied to reveal the wear mechanism. In addition, based on the central composite experiment method, the influence law of traction speed, drum rotation speed and spiral angle on the wear depth of drum, and the response functions between factors and pick, blade wear depth were obtained. Considering the drum wear depth and cutting performance, the Multi-objective optimization theory was used to determine the optimal working parameters. The results indicate that, the wear of pick and blade is most serious of the drum assembly. In the process of drum cutting, the pick, and blade wear depth increase with the traction speed. Moreover, with the increases of drum rotation speed, the pick wear depth decreases, and the blade wear depth first increases and then decreases. While, with the increases of spiral angle, the pick wear depth first increases and then decreases, and the blade wear depth decreases gradually. It is found that when the traction speed is 4.85 m/min, the drum rotation speed is 86.82 r/min, and the spiral angle is 13.8 ° the comprehensive performance of the drum is optimal. At this time, the load fluctuation coefficient is 0.1078, the cutting ratio energy consumption is 1.173 kW·h/m3, the pick wear depth is 0.002 mm, the blade wear depth is 1.37x 10-6 mm, the productivity is 303.098 t/h and the maximum cutting area is 1215.69 mm2.
KEYWORDS
Complex coal seam, Discrete element method, Drum, Multi-objective optimization theory, Wear and failure