Modelling interference fits and validating results
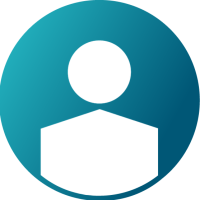
FredrikI_21476
New Altair Community Member
This article covers the modelling of interference fits/press fits using Optistruct and HyperWorks pre/post tools. The attached pdf "Interference_Fit.pdf" shows an example of how this can be done. To summarize the information in that pdf, the most crucial points are:
- Try to compare the radial stress of the FEM solution with the analytical solution for an interference fit available online or in multiple handbooks
- Use nodal averaging results (for example with HyperView) and the same measurement scale with equal nodal spacing as radial increments to plot the results in the same graph with HyperGraph or Compose
- Model the clearance with negative radial clearance and check with known standards that you are using the correct clearance
- Remember that the only non-linearity in this setup is the contact, the material is linear elastic meaning that you can get stresses way above yield in the elastic solution, you should see these in the analytical solution as well. If this occurs, revisit the problem and check the dimensions of the components, compare to standards and check the boundary conditions
- There will be differences in the FEM model compared to the analytical model since the analytical model doesn't capture the stress concentrations at the dimensional crossing between socket and shaft, there are also more BCs in the FEM-model that can cause stress concentrations and pressure differences. Also, the analytical stress is assumed zero at the entire outer boundary
Tagged:
1