Verification Example Comparing Hand Calculations to S-FOUNDATION Results for a Square Footing
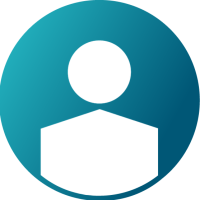

A Verification Example comparing Hand Calculations to S-FOUNDATION Results for a Square Footing
This document presents a simple foundation design example to demonstrate and verify the differences between performing hand calculations and using S-FOUNDATION to analyze and design the same foundation.
For this example, we design a square footing and compare the results from two methods:
A) hand calculations using CSA 2004 approach and
S-FOUNDATION's Rigid Footing approach.
The foundation has a 500mm square pedestal with loads applied concentrically on the pedestal.
- PDL= 900kN
- PLL= 1,200kN
The soil supporting the foundation has an allowable bearing pressure of 200kPa.
The material properties for the foundation are as follows:
- f’c = 25MPa
- fy = 400MPa
- φc = 0.65
- φs = 0.85
- Maximum Aggregate Size = 20mm
- Use 25M
- 75mm cover
A) Hand Calculations using the CSA 2004 approach
To begin, we first estimate the footing pad’s size.
Allowable Bearing Pressure (qall = 200kPa).
We assume the pad is square; therefore, A = b2
The square footing has 3.5m wide sides.
The actual bearing area is:
The Factored Load is: Pf = 1.25PDL + 1.5PLL
Therefore, the factored soil bearing pressure is:
Determine the footing depth, h.
Check 2 way-shear requirements:
Vf = Pf = 2,925kN
Determine concrete shear resistance for 2-way shear (Vc):
Using the 3rd criterion first, for determining (vc):
Determine d, based on 2-way shear requirements:
For a square footing:
Critical Shear Perimeter for 2-way shear (bo):
Now, let’s check the remaining 2 criteria for determining vc:
Third criterion governs. Use vc = 1.24MPa. Therefore, d = 0.56m.
Determine the footing depth (Using 25M bars, and 75mm cover):
Calculate d:
Check 1-way shear requirements:
Determine Concrete Shear Resistance (Vc) at critical section location:
Effective shear depth is the greater of:
β = 0.21 if:
Determine concrete 1-way shear resistance:
1-way shear demand:
To avoid shear reinforcement, Vf ≤ Vc
Vf = 835kN ≤ 1,208kN àNo shear reinforcement required
Check Flexure requirements:
Factored moment demand at critical section location:
Let Mr = Mf = 945kNm
Determine Steel Area Requirement:
)
Confirm minimum reinforcement satisfied:
As>Asmin > use 11-25M bars> As = 5,500mm2
S-FOUNDATION Rigid Footing design approach
When comparing hand calculations to S-FOUNDATION results, it is crucial to understand the difference in the approaches used by the two methods. Before we describe these differences, we will first discuss the modeling in S-FOUNDATION.
We edited the default Concrete Material (using Define>Materials) to reflect our Concrete Strength, and Max Aggregate Size.
We used the newly edited material in the definition of our pad and pedestal.
Reviewing our pad (Define->Pad/Pile Cap), we see the dimensions and reinforcement used.
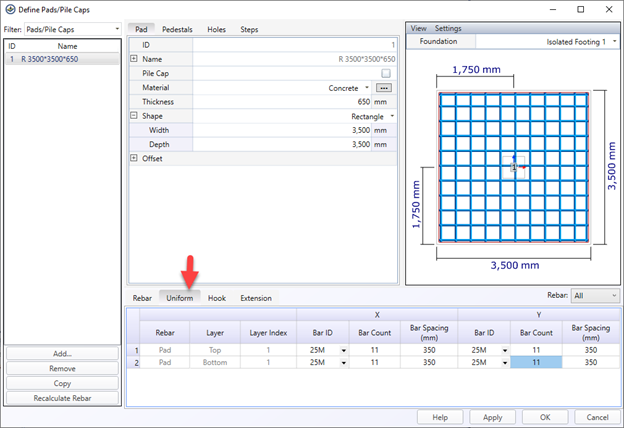
At this point, it is worth noting that the hand-calculation example considers the foundation in 2D only. S-FOUNDATION defines and evaluates the foundation in 3D, so that we have reinforcement in two directions (X and Y) and two layers. The S-FOUNDATION default is for the rebars in the X-direction to be located above the rebars in the Y-direction. Rebar layer ordering can be controlled in the Design Input Window.
For the pedestal (Define->Pedestal), we use a 500mm square section. The design of the reinforcement and the height is not relevant to the hand-calculations, so these values were assumed in the S-FOUNDATION model. We use a pedestal height of 1000mm and 10-25M vertical bars.
The Soil Profile properties (Define>Soil Profile) in S-FOUNDATION allow us to enter the Ultimate Bearing Capacity of the soil. The Allowable Bearing Capacity is the Ultimate Bearing Capacity/Bearing Capacity Factor of Safety. For your information, the Ultimate Bearing Capacity defines the maximum capacity of the nonlinear soil springs before they provide no further stiffness. For this example, we used an Ultimate Bearing Capacity of 600kPa and a Factor of Safety of 3 (Allowable Soil Bearing Capacity = 600kPa/3 = 200kPa). The Factor of Safety is defined in the Design Input Window under the ‘Settings’ tab.
Soil Profile properties (Define>Soil Profile) in S-FOUNDATION allow us to enter the soil’s Ultimate Bearing Capacity. The Ultimate Bearing Capacity is used to calculate the Allowable Bearing Capacity, defined as Ultimate Bearing Capacity/Bearing Capacity Safety Factor. The Ultimate Bearing Capacity is the maximum capacity of the nonlinear soil springs before they provide no further stiffness. In this example, we use an Ultimate Bearing Capacity of 600kPa and a Factor of Safety of 3 (Allowable Soil Bearing Capacity = 600kPa/3 = 200kPa). Define the Factor of Safety in the Design Input Window under the ‘Settings’ tab.
We create an Isolated Footing with our 3.5m square pad, 0.5m square pedestal, and assign the soil profile to the foundation.
We then create two load cases (dead + live) and apply the appropriate joint loads to the pedestal tip.
In the Design Input Window, you can also specify the clear cover for your reinforcement (75mm on the bottom of the pad), and choose which code checks to perform during the analysis and code checking process. For this comparison, we use the 'Rigid' Pad Structural and Geotechnical code checks. More information on the Rigid and Flexible Code Checks can be found in S-FOUNDATION’s Help System, but the reason for our choice here is that they are most comparable to hand calculations.
Remaining in the 'Design Input' Window, but switching to the 'Case/Combination' tab, we can control which checks are performed for specific load cases or combinations. We may not want to perform geotechnical checks for our factored load combinations, for example. If that is the case, we can always exclude them.
We then perform the analysis and code check (Run>Analysis and Code Check) so that S-FOUNDATION will generate the results.
Use the ‘Soil Bearing Pressure Tool’ to observe the calculated bearing pressure under our foundation due to the factored load combination.
As we can see, this number matches the value we calculated by hand. You may recall that opted not run the Geotechnical Code Checks for the Factored Load Combination. This result, however, is based on the structural analysis, but the Soil Bearing Code Check will be based on the load cases only, as we requested.
Review the ‘Design Output’ Window to see the results for each code check in more detail. The results highlighted are the governing results for each code check. Recall that our S-FOUNDATION model is considering the model in 3D space, whereas our hand calculation example is only considering 2D. This difference is the reason why some of the results in the graphic below may not match our hand calculations (the hand calculation is not evaluating those out of plane directions).
You can drill down into more detailed results by left-clicking the name of the code check (first column) or using the Code Check Tree.
Left-click the Pad Structural – One Way Shear (Rigid) results to investigate more details and we see two results (one for each axis). Note that S-FOUNDATION assumes the bars in the X-direction are above those in the Y-direction, hence the difference in effective depth. This can be controlled in the Design Input Window.
We will focus on the results in the direction which uses the effective shear depth = 506mm, since this matches our hand-calculations. For the CSA code, S-FOUNDATION find the one-way shear demand at the critical section location defined by dv away from the face of the pedestal. Given that we have a 3,500mm wide pad, a 500mm thick pedestal, and an effective shear depth of 506mm, the critical section locations for 1-way shear will be:
and,
From this location, S-FOUNDATION has determined the one-way shear demand is 830.6kN, and the capacity is 1,209kN. The small difference in the demand is due to the fact that our hand calculations rounded up the bearing pressure on the soil from 238kPa to 240kPa, whereas S-FOUNDATION uses the true bearing pressure under the critical section of the pad (237kPa).
Now consider the Punching Shear Results.
Notice that the 'Effective Depth' is slightly different from the value used in the hand calculations. Remember that S-FOUNDATION has two layers of rebar, and this effective depth is the average of the X and Y effective depths. The hand calculation assumes that all of the reinforcement is at the same depth (562mm). The slight difference in effective depth also yields a small difference in the punching shear perimeter; however, S-FOUNDATION has still found that the governing perimeter is for an interior pedestal. S-FOUNDATION’s calculated punching shear capacity matches that of the hand calculations.
For Flexure, we view the results in X and Y again. The only difference is the effective depths. If we examine the direction with an effective depth of 562mm, we see that the values are virtually identical to the hand calculations, which show that 11-25M bars are required.
The critical section location is the face of the pedestal and is shown in S-FOUNDATION as the distance from the leading edge of the pad. Since the pad is 3,500mm wide, and the pedestal is 500mm wide and concentric with the pad, the locations of the critical sections for Flexure are at 1,500mm, and 2,000mm respectively.
We also see our demand (940kNm) essentially matches the hand calcs (945kNm). The small discrepancy is, once again, due to the fact that the hand calculations round up the soil pressure to 240kPa, where S-FOUNDATION continues to use the exact value of 238kPa.