Contact adjustment of 1D Elements with 2D Surfaces
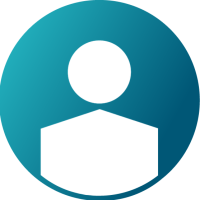
Hi guys,
Lets say I have a design space modeled as a geometry file. I have a set of cylinders modeled as 1D Beam Elements which should all lie within the design space box.
The idea is to use a contact adjustment calculation (=contact initializatio) between the cylinders and the design space.
I tried to model it with a two contact surfaces but the elements (1D) are not valid.... is this even possible to do with Hypermesh?
I wrote the problem with illustrations into the attached .pdf file.
Any help is greatly appreciated!
Thanks!
Merula
Answers
-
Hello,
attached is a model, that describes the contact definition using the 'adjust' option. To define a contact, you have a mesh of 2D Elements and an element set on the outside of your design space and a node set containing your 1D nodes.
The adjust Parameter needs to have the distance in which to search for the contact and then pushes all slave (1D) nodes to the shell. In the standard definition, the Shell Thickness is considered but not the 1D Diameter. So to avoid penetrations please set the PSHELL Thickness larger than twice your maximum Beam Cross section. In this video, the beam section is 7.7, so I set the PSHELL to 16 > 2x7.7.
The Pushout direction during the adjust is influenced by your Shell Normal direction, so you need to seht the 'MORIENT' option in your contact definition.
To get the final position, use the 'position' measure in HyperView or the corresponding OML or TCL language command in COMPOSE after reading your H3D results.
Jan
0 -
Here is the link to the video, explaining the contact definition:
https://www.screencast.com/t/nK1NO4swbn
0 -
Maybe Morphing with 'Map to Geometry' would be a faster approach to your task:
https://www.screencast.com/t/xSRuc0nQX
0 -
Thank you very much for this!
0 -
Altair Forum User said:
Hello,
attached is a model, that describes the contact definition using the 'adjust' option. To define a contact, you have a mesh of 2D Elements and an element set on the outside of your design space and a node set containing your 1D nodes.
The adjust Parameter needs to have the distance in which to search for the contact and then pushes all slave (1D) nodes to the shell. In the standard definition, the Shell Thickness is considered but not the 1D Diameter. So to avoid penetrations please set the PSHELL Thickness larger than twice your maximum Beam Cross section. In this video, the beam section is 7.7, so I set the PSHELL to 16 > 2x7.7.
The Pushout direction during the adjust is influenced by your Shell Normal direction, so you need to seht the 'MORIENT' option in your contact definition.
To get the final position, use the 'position' measure in HyperView or the corresponding OML or TCL language command in COMPOSE after reading your H3D results.
Jan
I just looked into implementing this. One problem I had is this:
When I have to define the shell element to be the element to define how much the beam gets pushed out, I would have to map the diameters to the shell elements (for different diameters). Is there a way to consider the 1D diameter?
Thanks in advance and best regards
Merula
0 -
You could use the 'GPAD' Option in your contact parameters, to define a certain thickness of the contact, derived from your beam section. This could be probably done automatically, using a script.
0