Altair Inspire® Challenge #2: Cycling Shoe Cleat Design
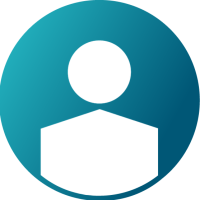

Road cyclists use plastic cleats on the bottoms of their shoes to create a constant point of contact between their feet and the pedals while riding.
These cleats are adjustable to accommodate different user’s preferences, and must also resist a combination of compression (downstroke) tension (upstroke) and twisting forces (engage/disengage).
This challenge is to come up with a design for a cleat that provides sufficient strength, and durability, while limiting the stack height (pedal thickness + cleat thickness + thickness of sole of shoes) and overall weight to please the most demanding weight concious cyclists. Assume a max normal force of 2500N during the downstroke, an uplift of 300N and a twisting forces. The model comes with a suggested design space, but can be adjusted to reduce the stack height, etc. if desired. The choice of optimization is up to you.
Tip: If you have trouble running an optimization, try running an analysis to ensure the model is behaving as expected.
Level: Easy
Product Required: Altair Inspire (including personal edition)
If you would like to solve more challenges and get regular challenge release updates, Subscribe to the Altair Community Challenge forum.
The solution can be attached in the comment section of this post. The desired output format is a set of PNG or JPG files showing the solution.
The solution to Challenge Bridge Concept Design can be found Here
Comments
-
Hi!
I could reduce mass by 25%, from 24g to 18g and also I reduced the cleat height from 13mm to 12mm (which is not much :c but still works) , resulting on this shape:
It also reduced maximum Von Mises on the combined loadings case from 172MPa to 103MPa, which results on the piece having more strength against the maximum loadings.
Optimized piece stresses:
Old piece stresses:
Thank you!
1 -
David Galvis_21599 said:
Hi!
I could reduce mass by 25%, from 24g to 18g and also I reduced the cleat height from 13mm to 12mm (which is not much :c but still works) , resulting on this shape:
It also reduced maximum Von Mises on the combined loadings case from 172MPa to 103MPa, which results on the piece having more strength against the maximum loadings.
Optimized piece stresses:
Old piece stresses:
Thank you!
Very nice, David!
0 -
Hi,
So, I was able to reduce the percentage weight reduction from 0.024 kg to 0.015 kg is approximately 37.5%.
1 -
Sourav Das_20575 said:
Hi,
So, I was able to reduce the percentage weight reduction from 0.024 kg to 0.015 kg is approximately 37.5%.
Very nice, Sourav!
0 -
Matthew Sauer_21269 said:Sourav Das_20575 said:
Hi,
So, I was able to reduce the percentage weight reduction from 0.024 kg to 0.015 kg is approximately 37.5%.
Very nice, Sourav!
Thanks Matthew
0 -
Hello,
In the meticulous pursuit of optimizing each component, an unwavering commitment to upholding a superior design structure emerges as paramount. Through judicious engineering, a remarkable feat was achieved, seamlessly reducing the mass of the component from 24 grams to a mere 16 grams. This feat was orchestrated through the strategic implementation of "Partitions" and the ingenious application of "extrusion" techniques, culminating in an outcome that radiates brilliance.
Astonishingly, The initial configuration yielded a displacement of 1.506mm, a value that underwent a profound transformation in the crucible of optimization, emerging as a trifling 0.1761mm—an achievement that stands as a testament to the power of meticulous refinement.
The original stress manifestation, quantified at 84.03MPa, pales in comparison to the elevated prowess demonstrated by the optimized version, which commands a formidable 119.1MPa.
.
.
Thank You!!
1 -
Kunal Pandit_21294 said:
Hello,
In the meticulous pursuit of optimizing each component, an unwavering commitment to upholding a superior design structure emerges as paramount. Through judicious engineering, a remarkable feat was achieved, seamlessly reducing the mass of the component from 24 grams to a mere 16 grams. This feat was orchestrated through the strategic implementation of "Partitions" and the ingenious application of "extrusion" techniques, culminating in an outcome that radiates brilliance.
Astonishingly, The initial configuration yielded a displacement of 1.506mm, a value that underwent a profound transformation in the crucible of optimization, emerging as a trifling 0.1761mm—an achievement that stands as a testament to the power of meticulous refinement.
The original stress manifestation, quantified at 84.03MPa, pales in comparison to the elevated prowess demonstrated by the optimized version, which commands a formidable 119.1MPa.
.
.
Thank You!!
Excellent work, Kunal!
0 -
Hi,
So I run some tests to optimize the structure, but it was not so easy to take something away. From the start model, it already bends 1,6 mm and von mises goes over abs limit (105 MPa). There was no mention about changing the material, so I stuck with abs.
Here is my optimize result:
So this is my result:
I got max displacment 2,18 mm and max von mises 123 MPa. The weight is now 21 g
PS.
I can’t understand how other have manage get rid of some much material and even get better stiffness.
1