Digital Twin for Durability
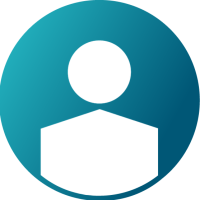

Product Evolution
Products are evolving, and so are the product development cycles, which are significantly influenced by data - large amounts of data! Today, data serves not only for validating virtual models, such as in digital twins used for system designs, but it also plays a crucial role during operations. Unlike in the past when companies would often lose touch with products once released, they now maintain a connection to them.
Indeed, modern products have the capability to transmit data - data used to assess their status, monitor performance, detect anomalies, identify potential unplanned working conditions and scenarios and so on. Data, data, data... it's everywhere!
This data is often processed by a "brain," also known as the “operational” digital twins that reveal critical insights. Sounds straightforward, right? However, deploying digital twins to uncover precisely the best actionable insights is only possible if you have the right technology partner.
Whether derived from simulations or sensors, today's challenge lies not in the availability of data, but rather in its efficient and effective utilization. Data is frequently tainted, incomplete, found in various formats, noisy, or even irrelevant. In practice, only a small percentage of the available data, after undergoing a thorough cleaning process, becomes eligible for processing by the "brain."
The Gold Life Cycle
To provide a straightforward explanation of the data flow in a typical scenario, I like to use the analogy with the gold life cycle.
The data generated by machines, vehicles, or other assets is like sediment found in a riverbed. To extract valuable insights, we require a tool like a gold pan, which sifts through the sediment to uncover precious gold flakes. This process mirrors data preparation, where we sift and organize the truly pertinent data.
Once we've prepared the data, we move on to processing it. During this phase, we enhance its value. Digital twins carry out the processing with either physics or AI-based techniques. Similarly, from the gold flakes, we can fashion a ring.
Once the gold ring gleams, it shouldn't be stowed away in a drawer; instead, it should be showcased. Likewise, the results generated by digital twins must be accessible through a suitable dashboard.
What our analogy doesn't capture is feedback. Indeed, based on the results obtained, we may opt to modify our products or their components, thereby enhancing them or refining the next generation. Unlike the riverbed, which remains unchanged, we can adapt and improve based on the insights gleaned from the operational digital twin.
Predictive Maintenance
Currently predictive maintenance represents the most prevalent operational digital twin, covering approximately 25% of applications. These digital twins work as virtual sensors monitoring physical assets in real-time, calculating indices such as the remaining useful life (RuL) or the state of health (SoH) of critical components.
They offer numerous benefits:
- Enhance safety
- Decrease downtime and associated costs
- Prolong the system lifespan
- Enable planned maintenance actions
- Facilitate root-cause analysis
- Enhance reliability that brings competitive advantage
They are straightforward to implement at the component level and can be applied across various domains including:
- Electric vehicles where the pursuit of lightweight designs to extend range escalates the risk of fatigue-related failures.
- Heavy Industry where components endure high loads due to material handling.
- Structural applications where structures must withstand dynamic loads from moving equipment such as cranes or wind loads impacting tall antennas.
The Future
Research predicts an average 40% compound annual growth rate for the digital twin market in the next ten years. This projected growth means an increase from 15 billion USD (in 2024) to 150 billion USD in 7 years.
Digital twins will be increasingly adopted to process sensor data from the field and transform it into a readable form by unveiling and augmenting its hidden information, for instance, calculating theoretical key performance indicators (KPIs), implementing corrective actions, and detecting system anomalies.
Partnering with the right software solution provider should meet two key requirements: First the provider must democratize the needed AI-powered technology so that users at any level of expertise can leverage it. Second, the solution partner must be genuine and trusted to guide companies through their digital journeys.
Altair provides the most comprehensive digital twin solutions, comprising best-in-class technologies that can be seamlessly integrated into established workflows. Additionally, Altair offers domain expertise—people! Indeed, beyond delivering software, Altair is foremost a company comprised of skilled individuals at your disposal to help you achieve your goals more efficiently!
Learn more about Altair's digital twin applications in our upcoming webinars.