Recipe for Success in Augmenting CAE with ML
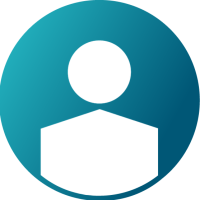

It was only when I started using pre-cut vegetables that my stews started looking and tasting better. Instead of spending time and energy on cleaning vegetables and cutting them into the same size and shape, I could concentrate on the things that really made a difference to the final result: improving the recipe, presentation and attending to the dish as it cooked. It might seem like quite a leap, but the lessons learned during my experiences in the kitchen proved useful when considering how to enhance CAE with Machine Learning (ML).
1. Using pre-cut vegetables improved my dishes. Using ML for preprocessing would ultimately improve designs.
In a typical CAE process scenario, an engineer receives a CAD file for a design. They will then spend a surprising amount of time cleaning up that file. The analyst will have to ensure that all the sliver surfaces are fixed, while paying attention not to close any actual gaps. All unnecessary features are deleted, and incorrect assembly hierarchies fixed. Then starts the process of identifying each part in the model, to allow the analyst to determine how to idealize them for the finite element analysis (FEA). Parts with large surface area to thickness ratios will be modelled as shell elements, others as solid elements. Bolts will be replaced with rigid elements and nuts will be replaced with thicker shells to reduce unnecessary model complexity. Further idealizations are required, for example welds or contacts; there are simply too many types to list. Once the task list is all checked off, the analyst must visually inspect the model to make sure the mesh quality is good enough for the analysis to be performed. For readers who have not meshed recently, please try and recall just how taxing this is on the eye.
2. Finite element models have to be visually inspected for model quality.
All these tasks steal the analyst’s focus. But what if we could reduce some of them? What if we could free the analyst’s time and energy for the tasks that matter most: exploring, generating and optimizing designs?
The good news here is that really significant time savings are within reach. Grouping parts by similarity avoids having to work part by part in a large model. Labelling the groups enables us to identify them next time we load a similar model. Once they are identified, modelling best practices can be consistently applied via automation throughout an organization. Let’s discuss each of these tasks briefly.
Clustering a dataset results in groups based on similarity. Clustering can reduce the time spend to create a finite element model (FEM). A typical FEM is made of hundreds, sometimes thousands of parts. Many of these parts frequently belong to only a handful of groups. Unfortunately, since parts are not consistently labelled in CAD/FEM files, it is hard to group them to operate on them group by group as opposed to part by part. This is why we need shape-based clustering. For example, an airplane wing FEM may have hundreds of parts, each belonging to a group such as ribs, rods, panels but not always consistently labelled as ribs, rods, panels in each CAD or FEM file. In these cases, grouping using shape-based clustering avoids the time-consuming need to work part by part in a large model (Fig.3). This will first require 3D shape representation and then clustering.
3. Clustering plane wing parts based on part shape.
Once parts in a FEM are grouped using shape-based clustering, this step can be eliminated in future projects using classification resulting in even more time savings. In this context, given a part shape, classification models will predict the most likely group that a new part belongs to. However, as mentioned earlier, classification requires labels. This neccesitates labelling the part groups from clustering. With the labels, we can then train a classifier model that will enable part identification next time a similar model is worked on.
4. A demo showing how classification works for FEA modelling.
We are almost at the end of the process. However, there is still one more thing that needs to be done. Once the parts have been identified, some need to be simplified to reduce model complexity. Specifically, this means identifying small features that are not necessary to mesh with detail. It could also involve identifying repetitive features that should be treated before meshing the larger model. Like clustering and classification part segmentation would also require 3D data representation followed by segmentation model training. An example of how segmentation works is given in image 5.
5. Segmenting a bolt to its head and shank.
Finally, once all the parts and features are correctly identified, finite element modelling using best practices can be consistently applied via automation throughout an organization. As a result, the benefits are multiplied across the engineering team.
Engineers are under increasing pressure. More innovative and efficient designs need to be completed faster than ever. As a result, we must take advantage of every opportunity to save time and improve outcomes. By recognising how much effort engineers currently expend on model preparation, and applying proven ML techniques to automate the tedious, ‘eye bleeding’ work that is involved, we can free more time for the real jobs of product design: exploration and optimization. In other words, we can allow engineers to be engineers. As far as I’m concerned, that sounds like a recipe for success.
Full version of this article can be found in NAFEMS Benchmark Magazine October 2021 issue at https://www.nafems.org/publications/benchmark-magazine/archive/october-2021/