Faster Simulation of real-world machines
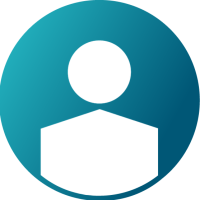

Simulation,
to meet machine builder' needs
In this article, I’ll be illustrating some development approaches that address challenges faced by the machine builder industry. With the help of my colleagues Daniel Jauss, Simon Zwingert, Felix Koerfer, and Christian Kehrer, we are showcasing how simulation-driven development enables better decision-making when developing new generations of machines.
Each detailed demo video gives you an overview and explanation as to how a scalable simulation solution helps you to improve overall system understanding: both the machine design and its control.
A key development goal of any machine-building project is to produce perfectly running, reliable machines that make high-quality products. By leveraging accurate virtual prototypes, seamless production can be ensured earlier in the development process to help assess and improve product profitability. If you develop processing & packaging, CNC-tooling, textile, special purpose machines or provide mechanical machinery engineering services, it is always the efficient interdisciplinary exchange between design and development departments that brings a machine’s structure, electrical, and control elements together in harmony:
- Simulation strategies need to ensure the quality of the final product by encompassing the entire process with all its variables, including the products produced by the machine.
- Accurate virtual prototypes that represent machine behavior to properly size drives and mechanics, safely increase cycle rates while maintaining accuracy, precision, and robustness.
- Durability and fatigue assessment to design for ease of preventative maintenance scheduling.
- System simulation to optimize control systems for faster commissioning
Simulating a CNC-Milling Machine
Here, looking at a 3-axis CNC-milling machine, Altair Simulation Solutions cover all these topics. We show how the evaluation of real-world machines becomes more comprehensive and leads to quicker and better development decisions. Depending on the stage of the development project, expanding the system understanding in early design phases increases the level of modeling detail and accuracy required as the design progresses.
As roles and responsibilities change throughout a development or implementation project, it is important to refer to a consistent technology basis throughout the organization.
Improve system understanding with dynamic motion analysis!
- Identify real behavior of the machine assembly
- Identify peak loads
- Identify drive torque
- Identify motor power
Image: Altair Inspire - Multibody analysis to identify motor power
Daniel Jauss, Application Engineer CAE, gives a demo explaining how to improve system understanding with dynamic motion analysis to reveal the actual behavior of the machine assembly and identify peak loads. Daniel takes us through the setup of a motion simulation within Inspire using real application movement profiles and walks us through validation and plausibility checks.
Accurate structural assessment with real loading conditions
- Assess global stress and deformations
- Evaluate bolt forces
- Improve accuracy & deformation
Image: Altair Inspire - Machine portal deformation
Felix Koerfer, Technical Consultant at Altair, gives a demo explaining how accurate structural assessment with real loading conditions allows evaluation of global stress and deformations and bolt forces to show how accurate predictions help to improve the product performance.
In the demo, Felix assesses the deformation that occurs during operation to increase the accuracy of the machine, considers stresses to potentially save costs or increase durability, evaluates connection forces to define the number and dimensions of bolts to improve the overall machine performance.
Improve the Design
with Studies and the Design Exploration
- Weld line optimization
- Design Studies on complete Assembly with parametric geometry
Image: Modal Analysis with Simsolid on the parameterized complete assembly
Simon Zwingert, Technical Consultant, gives a demo explaining how to improve the machine design with DoE studies and perform design exploration on the complete assembly.
Image: Identification of required weld lines with topology optimization in Inspire
Showcasing Altair Inspire topology optimization capabilities in the example of a weld line optimization, he identifies necessary weld locations and how to reduce the total weld length, to realize economic manufacturing alternatives.
Based on the CAD-Parameters defined in Altair Inspire Studio, he also conducts a design exploration in Altair Hyper Study to optimize the structural performance and improve vibration resistance.
Image: Design Exploration with Geometry Parameters
Vibration reduction with topology optimization
- Modal analysis & Optimization of a machine portal
- Identify economic manufacturing alternatives
- Topology optimization for sheet metal constructions
Image: Topology optimization for laser cut sheet metal structure in Inspire.
Daniel Jauss, Application Engineer CAE, gives a demo explaining how to reduce vibration with topology optimization by performing a modal analysis & optimization of the machine portal. His approach removes unnecessary material while improving the overall system performance. Using Altair Inspires’ motion and structure assessment ensures the functionality and the creation of manufacturable designs.
The method shows how to conduct a topology optimization for sheet metal constructions and quickly identify economic manufacturing alternatives.
CNC control optimization
- Toolpath optimization through tracking error correction of CNC milling machines, with system simulation.
- More effective controller design with realistic plant models
Image: Altair Activate PID-Control parameter tuning
Christian Kehrer, Business Development Manager System Modelling, gives an overview explaining how optimization of CNC controls is performed to realize toolpath optimization through tracking error correction of a CNC milling machine with system simulation and how to attain a more effective controller design with realistic plant models. In the example, Christian shows us how to improve speed and precision in mechatronics and control systems in Altair Activate. He demonstrates an approach for optimizing the dynamic interaction of multiple system components combining 3D finite element analysis, multi-body dynamics, and system simulation.
Summary
The increasing complexity of machines requires active management of technical risks in developing new product lines and especially in customer implementation projects. You can achieve this through multi-physics simulation and model-based development to understand the phenomena and root causes of unwanted behavior.
Altair simulation enables accurate virtual prototyping to help become more agile and independent of unforeseen external constraints. You can combine mechanical, actuator, and control engineering early on to find efficient and cost-effective solutions. To ensure perfectly running production earlier, Altair’s integrated product and process simulation tools come together to give a holistic view of the system.
"When you want to hear, what other users say about
the digital transformation for industrial Machinery,
and why they set simulation at the core of their development,
find here the recordings of our Industrial Machinery Technology Conference."