Product = GENESIS
Background of Topology Optimization in GENESIS
Topology optimization capabilities in the GENESIS software allow its users to improve practically any type of structures as most of finite element responses available in analysis (statics, normal modes, frequency response, heat transfer, buckling, acoustics, fatigue, etc.) can be used as objectives and/or constraints. In addition to FEA constraints, the users can also impose manufacturing constraint to get results that are consistent with desired manufacturing processes such as casting, stamping, extrusion and additive manufacturing.
Enforced Features
On certain occasions the user wants their final topology designs to contain specific features. Types of features include, but are not limited to: solid parts that can be used for connection and/or for aesthetics reasons and/or for imposing void sections (empty spaces) that can be used to pass through components such as tubes and/or other parts. Often such features are created manually by generating FEA meshes that include the desired features and made them non-designable so they stay on the final topology design. This frequently-utilized method is functional yet time consuming, especially when the design feature is not fixed on size or location and several concept meshes would be needed to represent different scenarios. Within this blog we will show that, in GENESIS, the design mesh does not need to be changed to impose a given design feature. In this blog we will show the results of two topology optimization runs: one design without any special features and another design with a circular design feature that could be used to attach a tubular component.
Example of Simple Topology Optimization Problem
In this example the objective function is to minimize the internal strain energy to get a stiff structure using 30% of the material.
Figure 1 shows: a) the designable space, in green; b) the load; and c) the boundary conditions. The load is a simple, concentrated force, acting downward at the top left of the design space. The boundary conditions consist of fixing the degrees of freedom of the structure at the corners of the right side.
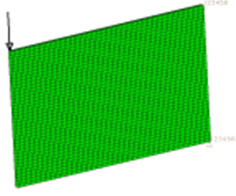
Figure 1
Standard solution of Topology Optimization
Figure 2 shows the final standard topology results where no special features were imposed.
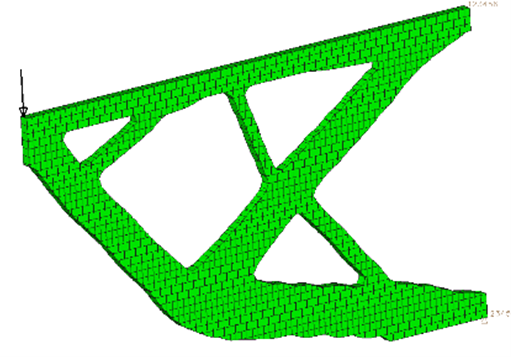
Figure 2
The final topology answer makes sense as the load can travel from the application point in the structure to its boundary conditions. This answer shows a familiar load path of this type of problem.
Cylindrical Part
Let us assume that we would like to connect the resultant structure with a component such as the cylindrical part shown in brown color in Fig. 3.
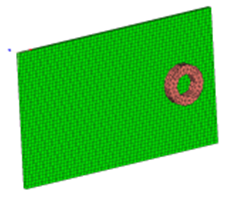
Figure 3
Topology Design without enforced Feature with a Cylindrical Part
Figure 4 shows the final topology and the cylindrical part of Fig. 3. From this picture, it is clearer that the topology results shown in Fig 2 would not connect the cylindrical part.
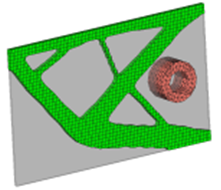
Figure 4
Topology Design with the enforced Feature
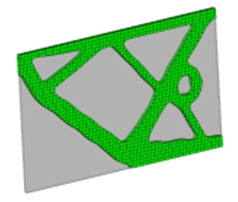
Figure 5
Figure 5 shows the final topology results with an enforced feature. This answer, like the free one in Fig. 2 shows that the topology can pass the load to the boundary conditions. But this second design, unlike the first one, can be connected with a cylindrical part as shown next.
Topology Design with the enforced Feature and with a Cylindrical Part
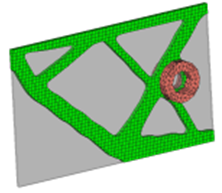
Figure 6
Fig. 6 shows that the final topology result allows the structure to be connected with the cylindrical part.
Note on how this problem was solved:
To obtain the topology result with special features, we used two capabilities in the GENESIS program: 1) Cloning and 2) Frozen Regions. The cloning capability, among other things, allows the users to project a topology region into another. In this case, we projected the 3D cylinder into the 2D planar design space. The cloning allows the user to use same design variables for the common parts and that makes the combined topology consistent. In this case, we did not want the 3D cylinder to be designed so we used the Frozen Region capability to force it to keep all its elements and by doing this, the common part of the 2D planar design region was forced to be kept, as well. In the next few paragraphs and figures, relevant steps are shown to illustrate the data creation process.
Step 1: Clone Cylinder into the Plate
In Step 1, we selected and designed the property of the cylindrical mesh as a clone of the main structure (parent). To do that, the form in Fig. 7 of Design Studio was used:
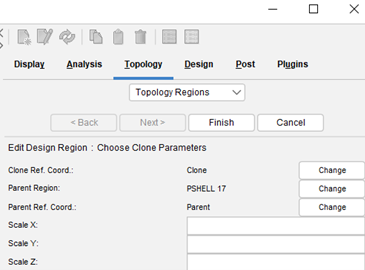
Figure 7
Step 2: Frozen Region
In Step 2, we selected all the elements in the cylindrical mesh as elements to be frozen. This is to force the elements of the cylinder to be kept by the optimization process. To do that, the form in Fig. 8 of Design Studio was used:
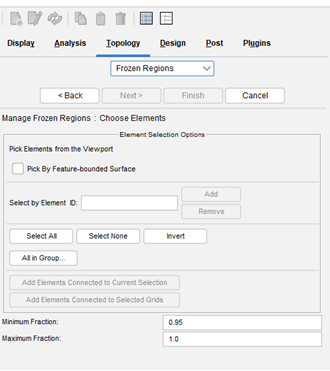
Figure 8
Summary
The GENESIS software can be used to obtain optimal topologies in which their final answers have specific features. In the example presented here, the special desired feature was to keep material in the design space, so as to attach a cylindrical component.
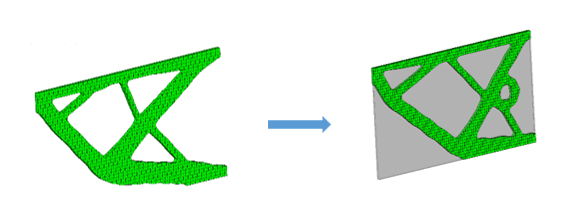
Figure 9
The structure in the left of Fig. 9 does not contain any special features. The embedded circular shape in Fig. 9 on the right is the desired enforced feature and is organically connected to the rest in the final design. The data needed to generate features for this problem was created using Design Studio and two key steps of the process were shown. To learn more about this type of problem, users can study the Design Studio’s step-by-step example manual or contact us for more information. If you currently do not have GENESIS and/or Design Studio, you can also contact us for more information on how to obtain them.
Connect with us now for complimentary webinars and evaluation software.
Our engineering team can work with you to conduct a Test Case showing how Genesis will improve your designs, processes and your overall business