Advanced Granular Material DOE and Optimization with Altair EDEM and Altair HyperStudy
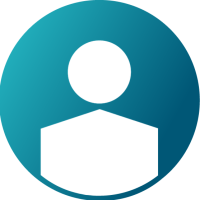

Originally Published : September 15, 2020
When using any CAE tool to understand a design or process, engineers look to perform design trade off studies to understand which parameters influence performance, eventually leading to optimized equipment and processes.
Users of the Discrete Element Method (DEM) are no different. It is well known that bulk material responses are, by their nature, complex and often show large degrees of variability. The large number of input parameters in DEM simulations also presents a challenge to engineers wanting to understand factors influencing overall system performance. This means having the right tools to analyze and explore bulk material equipment designs and processes is even more important.
Speaking with EDEM customers from many industries including heavy equipment, agriculture and pharmaceutical we always hear of three core optimization/design of experiment (DOE) challenges to address in the world of DEM:
Material Calibration – Modifying material, interaction and physics input parameters and measuring simulation responses with the aim of matching some know real-world response.
Process Optimization – Modifying kinematic and factory input parameters and measuring simulation responses with the aim of optimizing some process or system.
Geometry Optimization – Modifying geometry topology and measuring simulation responses with the aim of optimizing some process or system though geometry design optimization.
Being able to introduce intelligent automation that reduces the need for manual intervention and decision making, can significantly improve the above procedures. For DEM users this would mean quicker iteration to optimal material models, process conditions and equipment designs.
ALTAIR HYPERSTUDY
Altair HyperStudy is a design exploration tool for engineers and designers. It automatically creates intelligent design variants, manages runs, and collects data. Users are then guided to understand data trends, perform trade-off studies, and optimize design performance and reliability.
HyperStudy has been used for a long time by engineers who have, for example, wanted to perform design trade off studies for Finite Element Analysis (FEA) structural analysis problems. HyperStudy provides a smooth workflow for performing these kinds of studies and contains an abundance of DOE and optimization algorithms as well as tools for producing fitted reduced order models and tools for validating those models.
WORKING WITH EDEM AND HYPERSTUDY
At EDEM we have always had a focus on how we can help our users address the challenges listed earlier – particularly those related to material calibration. We have developed libraries of materials (the GEMM database, soils and powders starter packs), tools such as EDEM Cal for setting up large batches of DEM simulations, advanced post processing on the results through EDEMpy, as well as our unrivaled coupling capabilities with leading CAE tools.
Bringing the capabilities of HyperStudy into a workflow with EDEM offers value to many users faced with the challenges of calibration and system optimization.
Over the past months we have been exploring how we can work with HyperStudy to further interpret responses from simulations and discover trends or relationships in our data.
In a key first output from these investigations, we have produced a workflow based on a set of external tools that enable an automated exchange of information between EDEM and HyperStudy, and allow EDEM users to explore simulations and results in an entirely new way.
This initial workflow is focused mainly on material calibration, and enables the parameterization of all interaction and built-in physics input parameters. In addition, we have included some capability for process optimization with options for parameterizing a subset of kinematics input parameters (linear and conveyor; translation and rotation; velocity and acceleration kinematics).
The images below show a snapshot of the workflow for a process optimization example. Here we are looking at optimizing a mixing process. The image shows the input parameters in HyperStudy and the resulting fitted model. Using this workflow users are able to maximize mixing efficiency by selecting the optimum process conditions for running the mixer.
GET HANDS ON WITH THE EDEM – HYPERSTUDY WORKFLOW
We are excited by these initial tools and are already seeing them help in DOE and Optimization investigations. We would love to get more feedback on these tools and workflow to help us understand how we can continue to improve, and so we are making these available to our user community.
As well as the tools themselves, we have a User guide that outline the workflow, and two supporting examples which we are providing for you to get started. Customers can access those files directly from the Knowledge Base.