Altair Feko Coffee Break: Optimizing Radome Performance
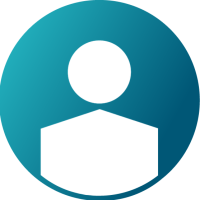
In this Altair Feko Coffee break, the performance of a radome is characterized and potentially optimized throughout each phase of the design cycle.
The performance of the radome stack including the dielectric layers and any potential Frequency Selective Surfaces (FSS) is first characterized using Periodic Boundary Conditions (PBC), which replicates the structure an infinite number of times in the XY-plane. The size of the unit cell, the physical dimensions and material properties of each layer in the radome can be modified with optimization algorithms to improve performance.
A characterized surface is then defined based on the transmission / reflection coefficients computed during the earlier phase. A characterized surface facilitates solving the electrical performance of an arbitrarily-shaped radome across multiple frequencies, polarizations, and angles with the Ray Launching - Geometrical Optics (RL-GO) numerical method. The physical details are hidden in this design phase, while RL-GO offers accurate yet blazingly fast simulations even when the structure is electrically-large.
After the material stack and radome structure has been characterized or even optimized in Altair Feko, Engineers can map the flat FSS model across an arbitrarily-shaped radome in a tool available in Altair Feko called newFASANT. A range of algorithms are available to assist with the mapping process depending on your needs.
Finally, newFASANT offers the Characteristic Basis Function Method (CBFM) to efficiently solve electrically-large models comprised of small details requiring a dense mesh. CBFM is available for both Method of Moments (MoM) and Multi-Level Fast Multipole Method (MLFMM).
Please watch the following video that showcases the features available throughout the radome design cycle.