Automating the Design of Crash Structures using Machine Learning
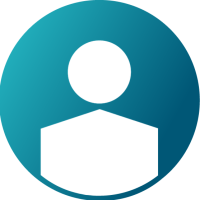

Crashworthiness is all about space. How much space is there in front of the occupant that can be intelligently filled with material? There are essentially two requirements that are conflicting; The vehicle should be strong enough to stop the vehicle from crushing before reaching the occupants’ legs but soft enough to prevent stopping too quickly leading to harmful deceleration. The more space available in the front, the easier it is to balance these requirements. So protecting the package space used for crashworthiness from other package requirements in the concept design phase is very important.
To protect your package space for crashworthiness, you must first calculate how much space you need to safely stop the vehicle. This can be calculated with kinematic calculations in a spreadsheet, using the allowable occupant deceleration and initial kinetic energy of the vehicle (calculated from the vehicle mass and speed). Once this has been established, the required crush force in the structure can be calculated from the deceleration and vehicle mass.
The next step is to design a structure that will provide the required crush force. A good way to understand what cross-sections to use would be to build component level Finite Element models of various cross-sections and axially crush them. Doing this manually for many variants would be time consuming, requiring model build, load case setup and analysis of each one.
What if we could use the power of automation and machine learning to make this process easier? In fact, we have proved this concept in a project called SectionAI. We used automation to take a sketch of a cross section and create the corresponding finite-element model and then run the analysis and post-processing. We also enabled definition of measurements (such as section height, width, thicknesses etc.) as design variables so that we could create Design of Experiments to generate data which could then be used to train machine learning models.
These machine learning models are then used to predict key performance indicators (KPI), such as mean and max crush force, as well as predictions of the entire force/displacement curve. We were then able to quickly and easily change the design variables to achieve the required crush force.
Even better, taking advantage of the fact that the machine learning models run extremely quickly, we were able to run optimization in near real time. This enabled us to search the design space for a section which would give the required mean crush force, or any other requirements whilst minimising the mass.
By using the automation and machine learning of SectionAI we were able to remove the manual process of creating and re-running an analysis for each cross-section variant. Now we can simply sketch a section and SectionAI will automatically produce data and generate machine learning models ready for exploration and optimization. SectionAI allows us to search the design space for the exact section to meet the requirements, and if those requirements change, we can simply run a new optimization using the existing machine learning models.
As a final note, we have been investigating the use of ShapeAI technology to predict unseen designs directly from the cross-section geometry without the need for parameterisation. However, this is a topic for another day. If you are interested in ShapeAI technology, read more about it in Doing More with ShapeAI in HyperWorks.
Please comment with any use cases you have that could benefit from automation and machine learning.