Mu_r distribution from spatial quantity causing 'isotropic BH required' error
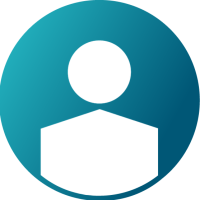
Dear all,
I'm currently investigating frozen permeability techniques for torque separation. I'm using the Macro for 2D Frozen Permeability. It exports the mu_r distribution for a specific operating point as a spatial quantity to a shadow project of the original project. A second call to the macro solves the shadowing model. In this second call, I get the error from the model telling
'Laminated magnetic non conducting region: the material must
have an isotropic B(H) property
Region STATOR: unsuitable material'. The same happens for the ROTOR region. Note that I did not touch the material definitions mad by the macro. I already changed the mesh to an extremely dense one, but this does not solve the behavior. I cannot further evaluate the spatial quantities in the unsolved shadowing model.
Are there any general recommendations towards using spatial quantities for this purpose, are is this maybe a macro-specific problem?
Any help is much appreciated!
Thanks in advance
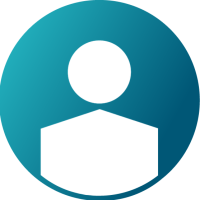
Hi Jelle,
In the second call of the macro, did you change the first setting from YES to NO?
What version of Flux do you use?
Best regards,
Alexandru
Hi Alexandru,
Yes, I select 'no' the second time I run the macro. My workflow is:
open model X -> solve scenario -> run macro in model X with Yes, shortname for final Flux project is Y -> change coil face region to air in model X -> run macro in model X with No, shortname for final flux project is Y
thanks in advance!
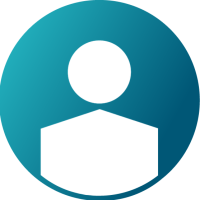
Hi Alexandru,
Yes, I select 'no' the second time I run the macro. My workflow is:
open model X -> solve scenario -> run macro in model X with Yes, shortname for final Flux project is Y -> change coil face region to air in model X -> run macro in model X with No, shortname for final flux project is Y
thanks in advance!
Hi Jelle,
Please try the next workflow:
open model X -> solve scenario -> run macro in model X with Yes, short name for final Flux project is Y -> change coil face region to air in model Y and edit the circuit associated to the model(delete the coils and sources from the circuit)-> run macro in model Y with No, short name for final flux project is Y.
The second run of the macro is done in the Flux project that results from the first run.
Best regards,
Alexandru
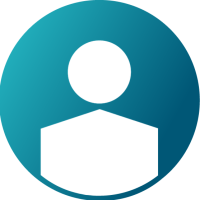

Hello Jelle,
How did you define the materials in the original project?
If you still have the problem, I suggest you to open a new ticket in the support section; so you can upload your original model in the there and we can have a look at it.
Best regards,
Letizia
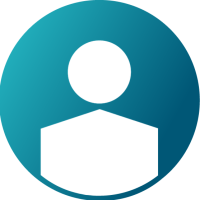
Hi Jelle,
Please try the next workflow:
open model X -> solve scenario -> run macro in model X with Yes, short name for final Flux project is Y -> change coil face region to air in model Y and edit the circuit associated to the model(delete the coils and sources from the circuit)-> run macro in model Y with No, short name for final flux project is Y.
The second run of the macro is done in the Flux project that results from the first run.
Best regards,
Alexandru
Hi Alexandru,
that's helpful! The material error is gone now, but now the macro crashes somewhere halfway. I will get back to that in a support ticket.
regards,
Jelle
Hi Jelle,
In the second call of the macro, did you change the first setting from YES to NO?
What version of Flux do you use?
Best regards,
Alexandru