QI mesh Creation
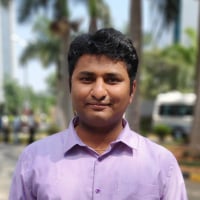

There are a lot of usefull information about meshing!!!
I'm meshing some parts using this info, specially the tutorial about 'QI mesh Creation' because I learned how to create and optimize a 2D mesh.
I have next questions:
1. How I can decide the element size???
2. Is necessary don´t have any 'bad element' to continue with the simulation?
I mean, when I check the elements in my mesh, all elements have to pass all criterias??
Answers
-
Hi,
1.Element Size
There is no thumb rule for an element size.
It depends on the Size & shape of the model , Type of analysis(Structural , crash, nonlinear or moldflow analysis) , computation time (hardware, etc).2.Element quality
Result quality ∝ Element quality
Ideal shape for quad elements – Square
Ideal shape for triangular elements – Equilateral triangle
Due to geometrical complexity it is very difficult to have ideal shape,so we have some relaxation range for different quality parameter like (aspect ratio, warpage , jacobian , min max quad anlge & min max tri angle, skew etc)By Default Optistruct solver check the element quality. Any violation of the error limits is counted as a fatal error and the run will stop. User have the option to deactivate the element quality check option.
Regards
Rahul R0 -
Brisa,
Just to add a little bit more to the excellent answer above,
If you are doing a linear static analysis etc element size can be very small,
regarding element quality It is not necessary to have a 100% good quality mesh, some elements can fail but we should try to never allow worst quality elements, element quality checks need to be balanced between the time you have and also how much the bad elements will affect your analysis, this can be learnt by experience, by validation of fea results with experimental results.
Engineers/companies doing serious FEA do have dedicated people just for meshing or spend a lot of time ensuring a good quality mesh.
with the right use of the quality and cleanup tools we discussed in HyperMesh you can quickly arrive at a close to perfect mesh most of the times, and you really need not compromise on mesh quality.
for eg as you are already doing, we can enter the necessary criteria in the criteria file as explained in the videos and then use the qi optimize meshing option, this will be a great starting point for a quality mesh, then use auto cleanup tools like smooth and elem cleanup,
So just continue with your projects and let us know the analysis type or send us snapshots of the model and we can guide you about the right element size and quality for those particular models,
As recommended for self learning in the homework section the HyperWorks student guide is a good resource for practical questions like this,
See for eg chapter 4 section 4.3 How to decide the element type
chapter 8 sections 8.2 General element quality checks and 8.3 2-D Quality checks
in fact entire chapter 8 is a must read0 -
HI,
I'm working in my own mesh
I have a metal lid and I need to review the deformation, so I used the next process to do the mesh:
1. Import the 3D geometry
2. Get the mid surface in order to do get a 2D geometry to mesh with shell elements.
3. Clean the geometry to avoid duplicates edges and too small features.
4. Mesh the geometry using several methods.
The first method was to mesh the geometry with the 'size and bias' option. Then, I check the quality index and I try to fix the mesh using the 'cleanup tools'. The QI changed from 2319.02 to 143.02The second method was to mesh the geometry with the automesh option and smooth option. The QI changed from 2321 to 1.02
Finally, the third method was to mesh the geometry with 'QI optimize' option . The QI was 2.01
As conclusion, the QI for second method and third method is much lower that the 143 value of the mesh that I get using 'size and bias'.I'm learning a lot about meshing!!!!
But I still have to learn how to decide the best element size option0 -
Hi Brisa,
Thank you for this report, this very clearly explains the necessity and the effect of using the QI panel and QI optimize. You are more than halfway into the requirements for a certificate !
Please continue working on this model which is your own, complete the linear static analysis and then review the results. Add all this information into a report (what you have posted in the forum here is a good start !) remember to explain what your model is about, the objective of this model, why did you perform this linear static analysis etc
please submit the full report here
https://securefiletransfer.altair.de/dropbox/~dle8l3. Submission is due on November 30, 2013.Good luck !!
0 -
Hi Mr. Rahul Ponginan
I'm a newest person working with HyperWorks. I have been started studying HyperMesh Tutorials module and QI Mesh Creation Section.
I have a little question about that. I'm using the model file, planar.hm for section. When I open model and go to QUALITY INDEX, the comp. Q.I is 3374.08, but in tutorial content written that:' On the right-hand side of the panel, note the value for comp. Q.I=. It should read 85.09'( see below figure). I feel may be have a prolem with my HyperMesh because in the same model and mesh presentation, but comp. Q.I is different between my computer and Tutorial Content. Please explain for me about this prolem.
Best Regards
0