Correct meshing of design and nondesign parts
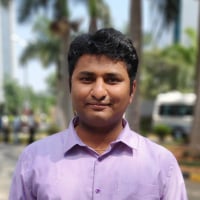

Hi,
I'm a new user of HyperWorks and have not much experience with the software. I want to optimize the structure of an aluminum cast part. The geometry (see picture) consists of the design part (black) and the nondesign part (white). The white parts are the holes for the screws and die white part in the middle is for bearings. So, all forces and constraints are attached to the nondesign parts.
I've created the geometry for the design and the nondesign part with a CAD program and import both in HyperMesh (as an assembly). By that I have two components in HyperMesh, consisting of 9 solid (1 black and 8 white). Then I meshed the volume with 'Create -> Tetra Mesh ->Volume Tetra' and select all solids. And optically it looks as if the meshes of the two components are connected completely. But when I start OptiStruct I get the following error:
*** ERROR # 312 ***
In static load case 1
the compliance is negative or large 1.452366E+14
Optimization/buckling analysis cannot be performed due to possible rigid body mode
Therefore I think that the meshes of the design part and the nondesign part aren’t correctly connected.
I hope you understand my problem and can tell me how to mesh the volume correctly. Tanks!!
Answers
-
Hi,
I would assume that the initial geometry volumes were not connected to each other, resulting in a disconnected mesh. To check this, it helps shading the geometry with 'By 3D Topo' option. You should see here yellowish faces indicating that two neighboring solids share a common face. If this is not the case, you could fix this on geometry level with boolean operations (page 'solid edit' -> boolean). You can also try to fix it on mesh level (using your already existing mesh), if you simply equivalence the dublicate nodes (assuming that they share the same locations) by using on page 'Tool' the 'faces'-functionality.Hope that this helps. Good luck & Regards.
0 -
I would suggest the following:
As I understood correctly, you apply force trough bolts on the non design space with RBE Elements ? I can not see any but I assume, you did that. As Permalink said, it is possible with solid edit -> boolean to merge all the solids into on and therefore connect all the surfaces. If this is not the case, then you could set up contactsurfaces (analysis -> contactsurfs), which are for each bolt 2 surfaces. The 2 surfaces can be matched together via the interfaces panel (analysis page). This method is important, if you do not want to apply the same property to all your components.
Further info about your load case and your bounding conditions would be helpful.
Good luck!0 -
It works
. Thank you!
0