What is the difference between using tie contact and shared nodes to connect different parts?
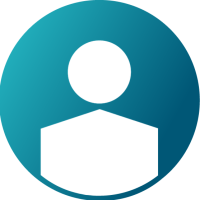
I'm trying to connect total of three parts like sandwiched together so if I use the tie connection I get the First mode frequency value very high and if I use shared nodes the frequency drop is very noticeable. So I want to know what is the difference between them and what should be used if the center part is acting like a Industrial glue that holds the other two parts?
Best Answer
-
You don't mention which solver you are using, behaviour may be different for different solvers in this scenario
You mention that the 'middle' component is a glue
If it is modelled as solids, many solvers do not have rotational degrees of freedom modelled at solid element nodes, if you use shared nodes this may have an influence on stiffness of the assembly vs using tied interface (that should pass the rotational degrees of freedom?)
If you are using shells, did you account for offset in both cases? i.e. did you model the parts with a gap when using tied interface and adjust offset accordingly?
0
Answers
-
You don't mention which solver you are using, behaviour may be different for different solvers in this scenario
You mention that the 'middle' component is a glue
If it is modelled as solids, many solvers do not have rotational degrees of freedom modelled at solid element nodes, if you use shared nodes this may have an influence on stiffness of the assembly vs using tied interface (that should pass the rotational degrees of freedom?)
If you are using shells, did you account for offset in both cases? i.e. did you model the parts with a gap when using tied interface and adjust offset accordingly?
0 -
Paul Sharp_21301 said:
You don't mention which solver you are using, behaviour may be different for different solvers in this scenario
You mention that the 'middle' component is a glue
If it is modelled as solids, many solvers do not have rotational degrees of freedom modelled at solid element nodes, if you use shared nodes this may have an influence on stiffness of the assembly vs using tied interface (that should pass the rotational degrees of freedom?)
If you are using shells, did you account for offset in both cases? i.e. did you model the parts with a gap when using tied interface and adjust offset accordingly?
I'm currently using Abaqus for solving
Yes the glue is modelled as solid but the top and bottom parts are shell, they have proper gap offset and thickness properties as per the need of my case.
Also it is true as per your answer when I use the shared nodes there is a influence of stiffness, But the overall stiffness of the model reduces, Whereas when I use tie the stiffness increases by a lot.
In my current case it seems there shouldn't be any rotational DOF acting between the parts so i went with the tie modelling, which seems to be accurate for my case.
Overall thank you for your response. If there is something you can say after reading my response it is much appreciated.
Thank you.
0