Design and Non-Design Space definition
Ok, what happens to me sometimes is that, depending on the constraints on the topology optimization, such as the % of volume required and the thickness constraint, I don't get back useful results and i don't understand why.
Can be relevant the dimension of the non design space? I mean, would it be different, as non design space, a plane thick 3mm o 30 mm?
thanks for the answer
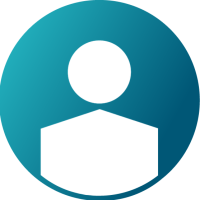
Try different combinations of mass & thickness constraints and use Shape Explorer to interpret topology results. Design space should be as large as possible to give optimizer a chance to find optimal topology. Non design space should only be used to apply loads and supports.
Use the Topology slider on the Shape Explorer to analyze the quality of your results. If the topology of your shape doesn’t change much when you move the slider, this means you’ve arrived at a good solution and may even be able to make your design targets a bit more aggressive. If the topology changes significantly when you move the slider, you should consider relaxing your design targets and rerunning optimization until the topology remains consistent when the slider is moved.
The optimal result is the point on the slider at which all of the load and support locations are just connected. When your optimization objective is to maximize stiffness, the optimal shape is generally found near the center of the slider marked by the star. When your optimization objective is to minimize mass, the optimal shape is often found to the far right of the slider.
https://solidthinking.com/help/Inspire/2018/win/en_us/shape_explorer.htm
Hi,
Ideally you want to use all the available packaging space as your design space as it has the greatest potential to give you the most optimal concept design. However it might not be possible to do so all the time. One of the factors that needs to be considered while creating design space from the packaging space is human and/or tool accessibility during manufacturing, assembly, and maintenance. An existing design is not a good package space to use for topology optimization. An existing design already has a material layout defined and so it is unlikely that it will yield to an optimal concept design.
After defining the design space from the available packaging space, it is also important to identify the non-design space. Regions in the model that cannot be modified during the course of the optimization are the non-design spaces. These are typically the connection points that connect to other components in the system or simply regions that need to exist for proper functioning of the system. These non-design spaces need to be identified beforehand to get a design that satisfies all the assembly constraints.
https://altairenlighten.com/opinion/five-common-mistakes-made-running-topology-optimization/
A design space can have any shape or topology as long as it is a single solid volume. A part that is used as a design space should not be very detailed. To ensure the most freedom to generate a shape, you should use the simplest design space possible. The more fine details you have in the design space, the longer it will take to run the optimization.
In general, it is best not to apply loads and supports directly to design spaces, as this often leads to incorrect results. Instead, you should split the part into design and non–design spaces and apply loads and supports to the non–design spaces.
https://solidthinking.com/help/Inspire/2017.1/win/en_us/design_space.htm