Hypermesh - Solidworks Weldments
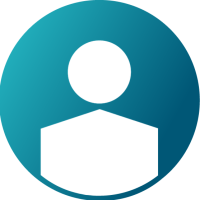
Hello everyone,
I'm new to this forum and hyperworks. So let's say I have this simple square weldment inserted from solidworks as a step file.It consists of 4 components and 4 solids. I meshed it using solid map -> multisolids option. I put some loads and some constraints and run the analysis. I realised that the 4 bars are not actually connected to each other. What would be the most simple solution to this problem? Either on SolidWorks or HyperWorks. Keep in mind that's not actually my problem, I have a whole car chassis to mesh. I just tried to simplify it.
Thanks for your time.
Answers
-
Hi Konstantinos,
There's a couple different things you could try, listed here in order of time to set up. If the model has a bunch of connected solids, you could use Boolean Combine to merge the solids together into something that could be meshed as one piece. This can be done in HyperWorks or CAD, but might be tricky if the solids aren't connected. If you have a large car chassis with a bunch of connections, a better solution might be to use Tie or Freeze Contact, outlined briefly in this and this blog post. These contact methods allow you to keep a linear solution if desired. Another way that would take the most time/planning is to equivalence the nodes at the intersection. Ensure the mesh at the intersection faces are identical, perhaps by copying 2d elements from one face to another, and then use equivalence through the edges panel.
Edges panel with 'preview equiv' and 'equivalence' underlined:
Hope this helps,
Christian
1 -
Christian Free_22016 said:
Hi Konstantinos,
There's a couple different things you could try, listed here in order of time to set up. If the model has a bunch of connected solids, you could use Boolean Combine to merge the solids together into something that could be meshed as one piece. This can be done in HyperWorks or CAD, but might be tricky if the solids aren't connected. If you have a large car chassis with a bunch of connections, a better solution might be to use Tie or Freeze Contact, outlined briefly in this and this blog post. These contact methods allow you to keep a linear solution if desired. Another way that would take the most time/planning is to equivalence the nodes at the intersection. Ensure the mesh at the intersection faces are identical, perhaps by copying 2d elements from one face to another, and then use equivalence through the edges panel.
Edges panel with 'preview equiv' and 'equivalence' underlined:
Hope this helps,
Christian
Hi Christian,
Thanks for your time, that really helped me a lot. I combined the chassis into one single solid in solidworks. Now what would be the best way to mesh it?
I have tried automesh commands (tetra and hex mesh). Both of them return errors without meshing it.
I start thinking that meshing each solid on its own and then connecting them with the connect command might be a better way than the single solid.
I attach the solidworks file below.
Thanks,
Konstantinos.
0 -
Hi Christian,
Thanks for your time, that really helped me a lot. I combined the chassis into one single solid in solidworks. Now what would be the best way to mesh it?
I have tried automesh commands (tetra and hex mesh). Both of them return errors without meshing it.
I start thinking that meshing each solid on its own and then connecting them with the connect command might be a better way than the single solid.
I attach the solidworks file below.
Thanks,
Konstantinos.
Glad that helped, but after looking at the model I think I understand the problem a bit better now. In a tube frame chassis like this, 3D meshing it will likely require many elements to be accurate (typically at least two or three elements through the thickness of a wall). It's also easy to run into 3d meshing issues in places where the tubes meet and the geometry isn't perfect. As such, a more common solution is to try a 1D mesh of the tubes, if it's an option. There's an article on this process here. An alternative if you have access to Altair's SimSolid software, you could use what you currently have to get a very quick solution, as outlined here.
0 -
Christian Free_22016 said:
Glad that helped, but after looking at the model I think I understand the problem a bit better now. In a tube frame chassis like this, 3D meshing it will likely require many elements to be accurate (typically at least two or three elements through the thickness of a wall). It's also easy to run into 3d meshing issues in places where the tubes meet and the geometry isn't perfect. As such, a more common solution is to try a 1D mesh of the tubes, if it's an option. There's an article on this process here. An alternative if you have access to Altair's SimSolid software, you could use what you currently have to get a very quick solution, as outlined here.
The thing is that I designed the chassis from an old book and dimensions of the plans are not perfect. So I know there are a lot of imperfect geometries.
So the second option you provided in your 2nd comment is not possible because I actually have to create a multibody with wheels, suspension etc.
The first option seems a little better for me.
What do you think of the idea of meshing each component separately (in the non-combined cad file) and then connecting them with connect command. Would this be possible?
Again thanks a lot for your time Christian.
0 -
The thing is that I designed the chassis from an old book and dimensions of the plans are not perfect. So I know there are a lot of imperfect geometries.
So the second option you provided in your 2nd comment is not possible because I actually have to create a multibody with wheels, suspension etc.
The first option seems a little better for me.
What do you think of the idea of meshing each component separately (in the non-combined cad file) and then connecting them with connect command. Would this be possible?
Again thanks a lot for your time Christian.
Meshing each component separately and later connecting them is certainly possible.
If you're referring to the Connect tool from the Connectors ribbon, I haven't looked very far into the tool but I understood it to be more about connecting concentric parts.
A couple options for connections that come to my mind: for a 1D mesh, you could connect things together using the RBE2 element/tool or simply connecting the nodes of adjacent beams. Another option I've seen is to 2D mesh the tubes with a midsurface and then connect the tubes together manually. A midsurfacing video is available here. Point connectors might be a good tool for connections and there's a video here. If you want to individually 3D mesh the tubes, check out the Auto Contacts button to help automate the process.
0