How to ensure ply connectivity between two half in composite shell model (PCOMPP)
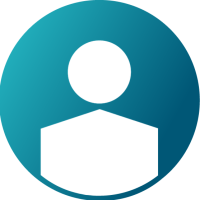
Hi,
I'm developing a composite model for the rotor blade analysis, where I import the Catia-designed geometry into HyperWorks using Simulayt. Within this model, the plies are realized separately in the top and bottom halves of the geometry, with layers stacked inside from the tooling geometry. While the leading edge (LE) exhibits geometry connectivity, there's a narrow gap at the trailing edge (TE). The plies are intended to close this gap as they stack the layers. However, when applying loads to the model, I notice that the trailing edge near the loading becomes separated. So my question is: does the ply contact between the two halves imply they are effectively glued together, similar to the production process? Or should additional measures be taken to accurately ensure the contacts simulate the gluing process?
Any suggestions are highly appreciated.
Regards
Ananthan
Best Answer
-
Hi Ananthan,
On the trailing edge of your composite, the nodes don't appear to be connected as there is a gap that you mention. So you need some kind of contact to bond the top + bottom together.
If you hadn't already, one way is to make a bonded contact on the trailing edge using TIE/FREEZE to bond the top + bottom plies together with contact surfaces and a CONTACT definition. Then you shouldn't see a discontinuity in the displacement plot because the top + bottom parts of the rotor blade will be bonded.
Thanks,
Rob H.
1
Answers
-
Hi Ananthan,
On the trailing edge of your composite, the nodes don't appear to be connected as there is a gap that you mention. So you need some kind of contact to bond the top + bottom together.
If you hadn't already, one way is to make a bonded contact on the trailing edge using TIE/FREEZE to bond the top + bottom plies together with contact surfaces and a CONTACT definition. Then you shouldn't see a discontinuity in the displacement plot because the top + bottom parts of the rotor blade will be bonded.
Thanks,
Rob H.
1 -
Hi Robert,
I'm sorry for not getting back to you sooner. The solution works perfectly with the mentioned contact.
Regards
Ananthan
0