Support location on a structural steel connection
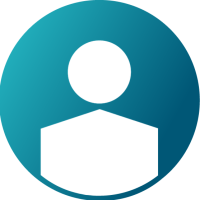
Hi! I am currently working on the optimization of a structural steel connection (Maximizing stiffness), but I have a doubt on where to place the support, as it is better not to be placed in the design space, and it is highly affecting the final optimization result.
I attached the original structural node, and the one to be optimized starting from a box-shaped node.
I appreciate any help related to where to place the support.
Thank you in advance.
Best Answer
-
if you know the load for each truss, you can try to apply all of them, and run an inertia relief analysis, with no support. IR will calculate the resultant load and try to compensate it to avoid rigid body movements.
But I would take take with the rotations at the joints, and how to model the connection points, and also what areas are designable or not.
0
Answers
-
if you know the load for each truss, you can try to apply all of them, and run an inertia relief analysis, with no support. IR will calculate the resultant load and try to compensate it to avoid rigid body movements.
But I would take take with the rotations at the joints, and how to model the connection points, and also what areas are designable or not.
0 -
Thank you for your reply! Your idea about Inertia Relief Analysis is very helpful, and I will try it.
The green area is the design space, while the yellow parts and the circular hollow tubes will remain unchanged as part of the non design space. I transformed the green area into a box-shape and then I am trying to perform the optimization analysis. The objective is to find a new design that can be 3D printed using AM.
For the connections points, I ignored the holes for the bolts to avoid stress concentrations in these areas. Moreover, the yellow parts and the design space are simply in contact.
I also appreciate if you have any idea that could be helpful on how to design the contact between the design and the non-design space.Best regards.
0