Coaxial feed excitation using FEM modal port
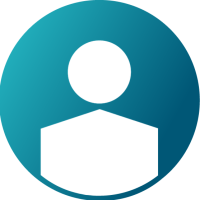
Hello,
I have been trying to excite the coax feed using a FEM modal port, however, I am seeing an error, which says 'Missing buffer zone for the FEM region when decoupling MoM and FEM'. Can somebody please help me understand what this error means and solution to this error ?
The outer cylinder of coax is copper and the inner cylinder is a pec.
Also, is there anyway in FEKO to accelerate meshing for large structures? Attached is the design that I am working on.
I really appreciate any suggestions or help.
Thanks.
Answers
-
Altair Forum User said:
The outer cylinder of coax is copper and the inner cylinder is a pec.
The reason for the error is that lossy metals (copper) is not supported on the FEM / MoM boundary. You need to either make the outer metal PEC or add an FEM air region around the metal so that the FEM / MoM boundary is the 'air' region that you add. However, looking at your model, I think the problem is rather the fact that the patches have losses and you will have to add an air region in front of the patches if you want to use FEM.
Have you tried using MoM for this model? Is there a particular reason why you want to use FEM?
Regarding the meshing, the only thing I can think of is that you can try to create a 'unit cell' of the patches and then mesh it. Once you have the unit cell, you can duplicate the mesh for the unit cell. This makes editing the model quite a bit more complex, but it is possible. If I were to do that, I would use scripting. I don't have any other suggestions. We are working on features that would (or could) make meshing these repeating structures easier in the future (but it is still early and in a concept phase).
Even with the meshing as you have it now, I'm not convinced the mesh is fine enough for accurate results. I would definitely do a mesh convergence study and also try a few solution methods and settings.
0 -
The only reason I decided to use FEM instead of MoM is the computational time and also I am only interested in the z-directed E-field, right above the patches. As you know, MoM calculates the impedance matrix and hence I would like to avoid that in my case to save computational time. Please correct me if I am wrong here.
But, thanks for the 'unit cell' suggestion, I will definitely give it a try.
0 -
Unless the structure is completely closed (waveguide or other non-radiating structure), it is difficult to predict what solution method would be the most efficient. You model does have a very thin substrate and that would lean towards FEM (usually). Since you have a radiating structure, you need to add a reasonably sized air box on the front of the structure (where the patches are). I would also use 1st order FEM, since you want to mesh fine. I hope some of these suggestion help.
0 -
Hi JIF,
Thanks for your suggestions. I tried out all the options you mentioned in your previous 2 replies. We tweaked the geometry from last time for faster results.
However, I could still not eliminate the feeding problem either with the outer metal as PEC or as dielectric material surrounded by air region. Attached are the .cfx and error message (.jpg) files for the both models. When using the dielectric material and air region, which face needs to be selected as FEM modal port?
Also, I am not aware on how to do a mesh convergence study. If you have any link, cfx file or attachment that explains about this study, please share it with me. I really appreciate your help.
--Kalyan
0 -
I didn't check your entire model, but the error in the image above is due to the fact that you changed Face17204 to PEC. It needs to be a dielectric boundary for the modal port to work.
For the non-PEC model, I'm not sure what the idea is with the cylinder that has not been unioned (probably need to delete it), but Face17205 would have to be change to PEC. If you want to make Face17205 metal (lossy), you will have to add FEM air around the outer coax.
A mesh convergence study refers to the process of reducing the mesh size until the results stop changing and can thus be considered converged. In order to do this, you first need to get your model to simulate. You can also first perform a model reduction study - remove parts of the model and see if they affect the results or not.
I see you are using version 14. I would (as always) recommend an upgrade to the latest version available.
0 -
Hi JIF,
Thank you for your timely suggestions and useful information. I really appreciate your help.
--Kalyan
0 -
Altair Forum User said:
Unless the structure is completely closed (waveguide or other non-radiating structure), it is difficult to predict what solution method would be the most efficient. You model does have a very thin substrate and that would lean towards FEM (usually). Since you have a radiating structure, you need to add a reasonably sized air box on the front of the structure (where the patches are). I would also use 1st order FEM, since you want to mesh fine. I hope some of these suggestion help.
Hi JIF,
Had some questions:
1) Able to share why you need the reasonably sized air box on the front of the structure? What is reasonable, say lam/2 thick?
2) Why would you recommend 1st order FEM? Is it because of the very thin substrate?
Thanks and best regards.
0 -
Hello CAW4933,
Altair Forum User said:1) Able to share why you need the reasonably sized air box on the front of the structure? What is reasonable, say lam/2 thick?
The reason in this case is that losses are not supported on the FEM/MoM boundary and thus the lossy face needs to be embedded in FEM (done by adding an air region around it). It is usually a good idea (for performance reasons) to keen the number of elements on the FEM/MoM boundary low and thus adding an air region can (often) reduce the number of FEM/MoM boundary elements because the air allows for a larger mesh size (larger wavelength in air vs. a dielectric). The size of the air layer is usually just to allow the mesh size to grow enough (to reduce the number of boundary elements), but half wavelength is a good suggestion (could be a bit less).
Altair Forum User said:2) Why would you recommend 1st order FEM? Is it because of the very thin substrate?
Correct. If you need to mesh fine due to the geometry, using first order mesh elements would be more efficient (less unknowns).
0 -
Altair Forum User said:
Hello CAW4933,
The reason in this case is that losses are not supported on the FEM/MoM boundary and thus the lossy face needs to be embedded in FEM (done by adding an air region around it).
Hi,
I am not sure if I understand you correctly.
I simulated two cases,
Run 1) Patch antenna with thin Substrate some over with FEM without the air box. Dielectric loss is higher than in Run 2.
Run 2) same model with Air box, with substrate and air is solved with FEM. but dielectric loss is lower than Run 1.
based on what I understand from your statement, the losses on the FEM/MOM boundary are not computer, so Run 1 dielectric losses should be lesser as it is not unaccounted for?
thanks.
0 -
Hello CAW4933,
My reference to losses were for metal losses. Thus, having a PEC face on a FEM-MoM boundary is fine, but having a Copper face on the FEM-MoM boundary is not supported. I was not referring to dielectric losses in the medium.
Regarding your discrepancy between the FEM and MoM losses, is the difference large or small?
0 -
Altair Forum User said:
Hello CAW4933,
My reference to losses were for metal losses. Thus, having a PEC face on a FEM-MoM boundary is fine, but having a Copper face on the FEM-MoM boundary is not supported. I was not referring to dielectric losses in the medium.
Regarding your discrepancy between the FEM and MoM losses, is the difference large or small?
Hi JIF,
Thanks for clarifying. So you were referring to metal losses, and not dielectric losses.
Both simulation runs were completed with FEM for the substrate, and I vaguely remember the losses differ by 30%, which seems quite large for a similar model.
Cheers.
0 -
Hello CAW4933,
Are you able to add the models, then I'll take a look? In some cases the power calculation can be very sensitive.
Thanks
0