Error 49 when simulating a winding in high frequency
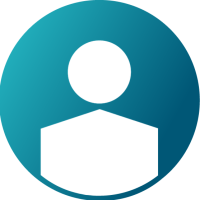
I am working in high frequency models, and as a starting point I made a winding with 20 turns with different core materials. To consider skin and proximity effects I draw a internal line in the conductor, to increase the mesh in that zone. However, even in 1 Hz, (when the mesh is not so fine), error 49 appears when solving.
Geometry, mesh and physics are checked and no error is shown.
I attach the flux project.
Thank you in advance for your help!
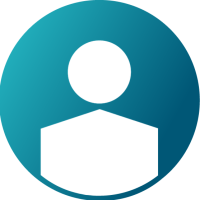
Hi Yerai,
I have analysed the project and I noticed a problem on the mesh of the air region around the device, the mesh is very loose, so it generated elements with very poor quality.
As first step I suggest you to replace the air box by an inifnite box in Flux, this infinite box will allows to close the FE element domain and imposed automatically boundary condition.
To create the infinite box you can use the menu Geometry -> Infinitie box -> New. For your project I suggest the following dimensions (parallelepiped):
Inner size: 100mm ; Outer size: 130mm
Once the box is created you have to complete it using the menu Geometry -> Infinite box -> Complete infinite box To mesh the box I suggest you to use a meshpoint of 15mm.
For the solving in the frequency range take care to adapt the mesh of the skin depth, I don't see in your project mesh information adapted to the frequency. For the high frequencies you want to solve as the skin depth will be very thin I suggest you to use solid conductor region described by surface impedance region instead of solid conductor region, it will allows to solve faster. You can find ore information about surface impedance in the help of Flux.
I hope this helps.
Best regards.
Cyril Favre
Hi Cyril,
Thank you for your answer. I cretaed the infinite box as you mentioned, but it still gives the same error at 1 Hz. Did it work for you?
Respect to the adapting the mesh to the skin depth, in the conductor I have 2 lines, the contour of the conductor, and an internal contour at the skin depth. In this way I ensure the mesh points in this area. Do you use another way?
I will try to use the surface impedance region for the highest frequencies, as you recommend.
Thank you very mcuh for your help!
Hi Cyril,
Thank you for your answer. I cretaed the infinite box as you mentioned, but it still gives the same error at 1 Hz. Did it work for you?
Respect to the adapting the mesh to the skin depth, in the conductor I have 2 lines, the contour of the conductor, and an internal contour at the skin depth. In this way I ensure the mesh points in this area. Do you use another way?
I will try to use the surface impedance region for the highest frequencies, as you recommend.
Thank you very mcuh for your help!
Hi Yerai,
Yes I was able to solve the project with surface impedance region in order to reduce the solving time. solve the project with solid conductors will need lot of memory and time.
Another remark in the project I suggest you to inactivate the aided mesh to avoid to have very long elements in the center of your rectilign conductors, it allows to avoid to have very poor quality of mesh due to this very long elements.
What is the main goal of your computation? probably you can try to simplify the model in order to reduce the computation time nd memory needed
I hope this helps
Best regards.
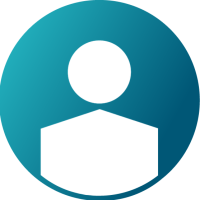
Hi Yerai,
Yes I was able to solve the project with surface impedance region in order to reduce the solving time. solve the project with solid conductors will need lot of memory and time.
Another remark in the project I suggest you to inactivate the aided mesh to avoid to have very long elements in the center of your rectilign conductors, it allows to avoid to have very poor quality of mesh due to this very long elements.
What is the main goal of your computation? probably you can try to simplify the model in order to reduce the computation time nd memory needed
I hope this helps
Best regards.
Hi Cyril,
Thank you for your answer. I will modify the mesh without the aided mesh to obatin a better quality mesh.
The final goal is to analyse a winding until 30MHz, but I am analysing a simpler case to adjust the model and try different materials on the core, to be sure i model them properly. I will simplify the model in the future.
Thank you for your help.
Best regards,
Hi Yerai,
I have analysed the project and I noticed a problem on the mesh of the air region around the device, the mesh is very loose, so it generated elements with very poor quality.
As first step I suggest you to replace the air box by an inifnite box in Flux, this infinite box will allows to close the FE element domain and imposed automatically boundary condition.
To create the infinite box you can use the menu Geometry -> Infinitie box -> New. For your project I suggest the following dimensions (parallelepiped):
Inner size: 100mm ; Outer size: 130mm
Once the box is created you have to complete it using the menu Geometry -> Infinite box -> Complete infinite box To mesh the box I suggest you to use a meshpoint of 15mm.
For the solving in the frequency range take care to adapt the mesh of the skin depth, I don't see in your project mesh information adapted to the frequency. For the high frequencies you want to solve as the skin depth will be very thin I suggest you to use solid conductor region described by surface impedance region instead of solid conductor region, it will allows to solve faster. You can find ore information about surface impedance in the help of Flux.
I hope this helps.
Best regards.
Cyril Favre