Problem with Solid/Shell Mesh Composite Sandwich
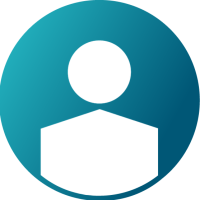
Hey guys!
I have a problem with my Sandwich model in Hypermesh (Nastran). I am looking for a solution for quite a while but all other related posts did not help me with my issue.
My model is a sandwich structure (HC core with CFRP plies on both sides) and I need the shear stress inside of the HC core. Therefore I am modelling my core as a solid and the plies with PCOMPG attached to the solid core. I checked all the elements for connectivity/dublicates as well as free edges and faces but I cannot find the problem in my mesh. Every time I run the model Nastran gives me the error "USER FATAL MESSAGE 9050 - RUN TERMINATED DUE TO EXCESSIVE PIVOT RATIOS IN MATRIX KLL" and I know that there has to be a problem with either my mesh or my constraints. I fixed the outer face of the model in all dof and the force is attached to the center nodes. (I modelled it with an rbe3 element as well but I wanted to make sure that that's not part of the problem). Therefore I don't think that my model is not properly constrained (I ran a pure shell model as well and that one works just fine).
Here is a picture of my HM model:
I ran a modal analysis but it did not produce any results since the analysis ran out of memory so I could not check for rigid body movements.
And here is what I get when I run the analysis (101) with param, bailout, -1 (solution of the CFRP sheets looks good, so the picture shows the core by itself):
So I know that it has something to do with the solid core nodes (two different honeycomb structures (red and pink) as well as a carbon insert (blue) but I cannot figure out what's the issue. Most nodes look like they have very little stiffness but are connected (looks like a cone) but some do really weird stuff.
Do you maybe have an idea what I need to check or how I could identify the problem? Maybe you guys even now right away what's the issue.
Thank you so much in advance!
Edit:
I ran the analysis with the hc core as Mat1 (isotropic material with the same properties as before) and everything worked well. So it looks like it is not a mesh problem but rather some solid element / material property thing. Before that I modeled the two different honeycomb solids with MATORT but that always ends up with the Error I described in the beginning.
Which Material Model would be the best to set up all the properties of an aluminium honeycomb in all three directions?
Hello,
It definitely looks like you have an issue with model setup (connection/constraints/material)
Since it is an Aluminum core, I would just use MAT1 since the properties should be basically the same in all directions.
I would refer to these articles for some basic debugging tips for future reference
https://community.altair.com/community?id=kb_article&sysparm_article=KB0121715
https://community.altair.com/community?id=kb_article&sysparm_article=KB0121263
https://community.altair.com/community?id=kb_article&sysparm_article=KB0121264
I would also recommend this great video series on composite modeling in hypermesh