topology optimization with a certain displacement applied
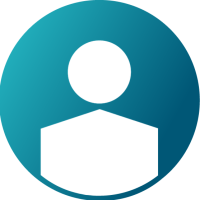
Good night dear all.
I am looking for some help.
Look i have a cylinder the cylinder with two NON-Design plates, one at the bottom and one at the top (of course the cylinder is the DESIGN part). Then the bottom plate is fixed with 0 displacement and rotations and the top plate suffers a -1.0 mm compression in the Z direction.
Note: the bottom plate has an SPC and the top plate has an SPCD, and the load step is linear static
With that being said i want to optimize the cylinder, having such displacement -1.0 mm in the linear regime of course, and minimize the volume.
i tried the following tutorial "OS-T: 2010 Design Concept for an Automotive Control Arm" with my own modifications, however, i getting non sense results (the whole design part disappears).
Finally, i was wondering how to do a topology optimization setting a desire displacement?.
In the attached file you will find the FEM file.
Thanks in advance.
Alberto Campuzano
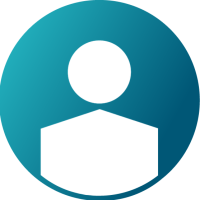
The way the model is set up currently, your design constraint is to have the plate move a maximum of 1mm, you are also prescribing a movement of 1mm on the node. So in fact the result makes total sense, the cylinder (and even the supporting base), aren't needed at all, the top plate will move 1mm whatever else is there, as you have told it to move 1mm. So the minimum volume is 0.
To get a reasonable topology result, I would approach it by Instead of prescribing a motion (SPCD), apply a load to the top plate and constrain the motion to 1mm.
Alternatively, if you had a 'baseline design' that you are trying to improve, you could use force/load from that as a guide.
In the quick example here I added a load of 1000, but the actual value doesn't matter too much, topology is just about getting a load path, you can size the detail the design after you get a material distribution.
This seems to converge to a set of columns!
Dear Paul
Thank you
I got the whole point, now everything works, thanks a lot.
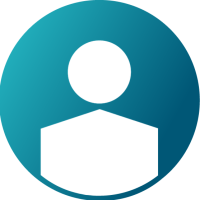

The way the model is set up currently, your design constraint is to have the plate move a maximum of 1mm, you are also prescribing a movement of 1mm on the node. So in fact the result makes total sense, the cylinder (and even the supporting base), aren't needed at all, the top plate will move 1mm whatever else is there, as you have told it to move 1mm. So the minimum volume is 0.
To get a reasonable topology result, I would approach it by Instead of prescribing a motion (SPCD), apply a load to the top plate and constrain the motion to 1mm.
Alternatively, if you had a 'baseline design' that you are trying to improve, you could use force/load from that as a guide.
In the quick example here I added a load of 1000, but the actual value doesn't matter too much, topology is just about getting a load path, you can size the detail the design after you get a material distribution.
This seems to converge to a set of columns!
The way the model is set up currently, your design constraint is to have the plate move a maximum of 1mm, you are also prescribing a movement of 1mm on the node. So in fact the result makes total sense, the cylinder (and even the supporting base), aren't needed at all, the top plate will move 1mm whatever else is there, as you have told it to move 1mm. So the minimum volume is 0.
To get a reasonable topology result, I would approach it by Instead of prescribing a motion (SPCD), apply a load to the top plate and constrain the motion to 1mm.
Alternatively, if you had a 'baseline design' that you are trying to improve, you could use force/load from that as a guide.
In the quick example here I added a load of 1000, but the actual value doesn't matter too much, topology is just about getting a load path, you can size the detail the design after you get a material distribution.
This seems to converge to a set of columns!