Does the choice of solvers lead to variations in results of KnC Analysis?
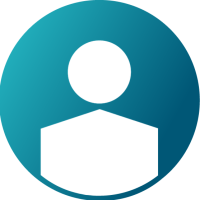
Greetings,
I've developed custom half car models for both front and rear suspensions, and successfully simulated them for all Kinematics and Compliance (KnC) analyses.
These tests were conducted using the same model through an outsourced service provider who utilized Adams Car software. They've provided all result files, and upon comparison, I've found that my results closely match theirs for static suspension design parameters such as KPI, Caster, Trail, and Scrub radius. However, there are significant differences in parameters like ride steer, roll steer, anti-squat, anti-lift, roll center height, ride rate, and similar metrics.
There are also some similarities in parameters such as wheelbase change during wheel travel.
How can we assess our development capability and validate our analysis process?
Best regards,
Sudip Chavan
Answers
-
Hi Sudip,
For simple simulations, such as half-car kinematics and compliance events, the differences should be negligible. In these events, the motions are relatively slow and controlled which should produce predictable and repeatable results.
In order to validate the two models and compare performance, I would start simple.
Have you completed a model review and confirmed the following are identical between the two models?
- Locations of all hardpoints
- Physical properties (total mass/COG/inertia, individual mass/COG/inertia)
- Spring/damper/bushing properties (stiffness/damping)
- Compression/Extension stops (engagement points, force curves)
- Event procedure (jounce/rebound stroke lengths and speeds, applied force vectors/magnitudes)
Once all of those are confirmed, the next area to investigate would be how measurements are taken. I would then create my own Outputs/Measures to confirm the position of hardpoints throughout the event to make sure the models are experiencing the same event the same way. For example, I would track the wheel end displacements in X, Y, and Z throughout the event and make sure they match. This is essentially the input to the model so it is the most important to match first. I would then pick another point after the wheel ends, such as the strut lower hardpoint, and track that through the simulation as well to confirm the model is experiencing everything the same way.
Therefore, if the properties of the model match and the displacement of key points/markers match, then the differences can simply be from how the automatic measurements are being taken. If your custom model does not have the correct markers being used for measurements, then you will see errors in the SDS calculations. Also, the ADAMS measures may be done differently than what the correct SDS calculations produce if they have an error in their expressions.
It is important to narrow the scope as much as possible, which is why I recommend starting with the basics.
Hope this helps!
Adam Reid
2 -
Adam Reid_21142 said:
Hi Sudip,
For simple simulations, such as half-car kinematics and compliance events, the differences should be negligible. In these events, the motions are relatively slow and controlled which should produce predictable and repeatable results.
In order to validate the two models and compare performance, I would start simple.
Have you completed a model review and confirmed the following are identical between the two models?
- Locations of all hardpoints
- Physical properties (total mass/COG/inertia, individual mass/COG/inertia)
- Spring/damper/bushing properties (stiffness/damping)
- Compression/Extension stops (engagement points, force curves)
- Event procedure (jounce/rebound stroke lengths and speeds, applied force vectors/magnitudes)
Once all of those are confirmed, the next area to investigate would be how measurements are taken. I would then create my own Outputs/Measures to confirm the position of hardpoints throughout the event to make sure the models are experiencing the same event the same way. For example, I would track the wheel end displacements in X, Y, and Z throughout the event and make sure they match. This is essentially the input to the model so it is the most important to match first. I would then pick another point after the wheel ends, such as the strut lower hardpoint, and track that through the simulation as well to confirm the model is experiencing everything the same way.
Therefore, if the properties of the model match and the displacement of key points/markers match, then the differences can simply be from how the automatic measurements are being taken. If your custom model does not have the correct markers being used for measurements, then you will see errors in the SDS calculations. Also, the ADAMS measures may be done differently than what the correct SDS calculations produce if they have an error in their expressions.
It is important to narrow the scope as much as possible, which is why I recommend starting with the basics.
Hope this helps!
Adam Reid
Thanks Adam,
I will narrow it down and will analyze results again.
Thank You.
0