How to check the frequency of the B field in the rotor of induction machines using a sensor?
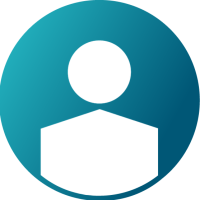
Dear all,
I am simulating a loaded four pole induction machine using a voltage-driven (sinusoidal) transient 2D simulation in FLUX.
When I check the B field in the stator iron (using a sensor), its frequency spectrum contains the fundamental supply frequency, e.g., 50 Hz, + harmonics due to slotting effect. In the rotor iron, I would expect the B field to vary at the slip frequency + harmonics. However, the spectrum of the B field in the rotor iron, calculated using a sensor, contains a fundamental component of 24 Hz + harmonics. So, it seems that the B field in the rotor iron is computed and therefore displayed in the stator reference frame.
The rotor currents instead have a fundamental component which varies at the slip frequency (that's of course correct).
Is there any possibility overcome this issue? maybe defining the rotating mechanical set in another way? To setup the simulation, I followed the examples provided with the software.
Thank you in advance for your help and support,
Marco
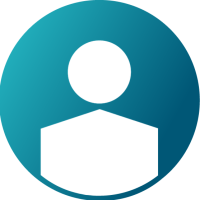
Dear Farid,
thank you for your answer.
Yes, I tried to do that and, as I already reported in my reply to the previous question, apparently I can't select a mechanical set different than STATOR: so, I can only select a fixed mechanical set.
Unless I should set some parameters when defining the moving mechanical set prior to solving the simulation, I have no idea on how to overcome such issue. I attach for you a picture of my mask.
Any other ideas?
Regards,
Marco
Hello Marco,
You are right, i tested what i suggested for you but it is not working.
The workaround i can propose you is to use a Path (of two points) for instance, so you can plot the quantity you want for a given time step, if you want to see a time variation on the path, so you have to plot a 3D curve on the path.
This path is created on the rotor, but will be fixed in the same location
This path is created on the rotor, but will be fixed in the same location
Regards
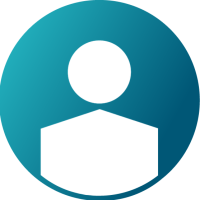
Dear Farid,
thank you very much for your suggestion.
So, I also suppose that it is not possible to extract a quantity, e.g., Bx and By, at the centroid of each mesh element on the rotor in a rotating frame.
I tried to do so using the macro ExportAreaAverageValue.PFM and after an FFT analysis it seems that the quantities (Bx and By) on the rotor were extracted in the stationary reference frame (fundamental frequency 24 Hz + harmonics). As mentioned above, I was expecting that the fundamental component of B on the rotor was the slip frequency.
Any ideas for this issue as well?
Thank you again and regards
Marco
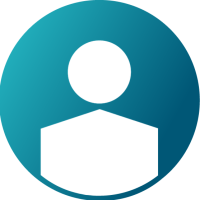
Dear Farid,
You mean carry out an export on multi point support using the macro ExportAreaAverageValue.PFM?
Do you mind telling me how to proceed?
Regards
Marco
Hello Marco;
Have you tried what i suggested you in your previous question ?
Rotor electrical frequency at no-load in induction machines simulated in FLUX 2D - Flux - Altair Products - Altair Community
Regards