Modal Analysis with Rigids
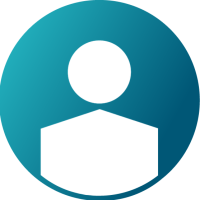
Hi,
I am trying to connect the beam modelled as 3D elements to the composite plate. Is there a faster way to do this? I tried using spot connectors and it did not work...
It turns out that the reason connectors are not working well is because I am running a modal analysis. Can anyone explain why rigids cause problems in modal analysis?
.
Answers
-
It depends on how you are setting up your model. The main issue is the DOF mismatch. For example, solid elements have 3 DOF's at each node while OptiStruct shell elements have 6 DOF's per node. In addition, based on whether you are using RBE2 or RBE3, (multi point constraints) the dependent and independent behavior that connects the two parts will also change.
When you connect a solid to a shell, without taking into account the DOF, you can end up with the unsupported component exhibiting spurious behavior.
A few of ways of overcoming this issue are: 1: You can use beam/bush elements instead of rigid elements. 2: you can use membrane skin elements on the solid. 3: using tied contacts.
Of course there are other ways too that simulation engineers have come up with over the years. Based on your experience one could work better than the other. Would have to try them out.
0