Can't mesh a face (error 18167)
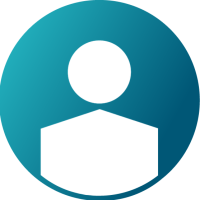
Hi everyone,
I am very new to FEKO and I am trying to use it to calculate the magnetic flux density produced by some planar coil. I run into an error when trying to mesh my model. I tried to attach a screenshot, but it won't accept my link... The model basically comprises of a copper layer (20 micron) on top of a glass layer (1100 micron). The top face of the glass, which borders the copper layer can't be meshed (error 18167)
Answers
-
Have you tried 'choose files' for the screen shot?
0 -
Hi Mel,
Thanks, somehow I did not see that in my first post. I have attached the file, hopefully somebody is able to point me in the right direction?
-edit:
Somehow I also did not get updated with new posts in my thead, so sorry for the late reply
0 -
The finite thickness is probably the cause.
This model will take a huge amount of resources due to the finite thickness.
Delete the redundant faces and with work with infinitely thin faces rather.
Also use the Simplify operator to reduce the number of redundant regions - Simplify will remove faces between regions of the same type, among other things.
0 -
Hi,
Thanks for the quick response. I have used the simplify operation, but the same face keeps giving the error. It is the top dielectric face (glass_pyrex) on which the 20 micron copper layer rests.
Regarding the thickness, how should I set the face thickness to infinitely thin? Or should I replace the 20 micron copper layer with just planes, representing the 'top view' of the copper?
Inside my glass substrate is a microfluidic channel and I would like to model the magnetic flux density that is produced by the coil in the channel volume. Therefore I think it would not be useful to reduce the thickness of the dielectric layer? Any tips are very much appreciated!
0 -
The PEC parts you can just delete the faces not directly touching the dielectric, the 'top' faces if you may.
The dielectric, yes, should remain an enclosed volume ('Region' in details tree).
If you look at the patch antenna or microstrip examples in the Examples Guide you will see the PEC faces are infinitely thin, touching the dielectric, but the dielectric is an enclosed volume.
0 -
Here as an example, I have removed some, not all, of the 'redundant' metallic faces. I refer to them as 'redundant' since the electrical thickness at 500 MHz is very very small. It may be that in the spiral the finite thickness does play a role due to the small spacing between the 'rings'. So it's best to test these assumptions with sub-parts of the model that can be solved faster.
0 -
Hi,
Thanks for the explanation. I have made a new model with just a glass layer and a 2D spiral, but I still get errors when meshing. I have again attached my model. I really don't understand what I am doing wrong here..
0 -
There is a problem here in the meshing. It is under investigation.
0 -
Thanks a lot, I will try this method and let you know if it works. Do you know why the 'normal' way is not working and splitting is?
0 -
Hi @SanderBash
Geometry like spirals and helices seem to provide a challenge for the algorithm used by the meshing library. Splitting the structure simplifies it just enough for the algorithm to work. Improvements have been made in previous versions of CADFEKO (including 2018.1 and 2019.2) and will be made again. The 'normal' way of meshing should work and the developers will have to look at what's going wrong.
0 -
Alright, thanks a lot. I have been using the working-at-home time to learn a bit about simulating B-fields produced by our coils. In general I find the software quite easy to use and the support forum has been very helpful!
The splitting trick has also worked for meshing the 3D coils it seems, I am running the solver now. Thanks again for the help.
0