Initial Rotational Velocity
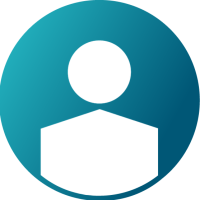
Hi,
firstly, let me introduce myself. My name is Javier and I'm a new user.
I'm trying to solve a rigid body problem on MotionSolve. The problem is a classical mechanics problem to study rolling without slipping (see attach picture for problem definition).
I'm trying to give a cylinder an initial rotational velocity about its longitudinal axis and then analyze if the cylinder will lose the contact force when it finds a plane that forms an angle of 30 degrees with respect the initial horizontal plane.
The contact seems to works nice, although I find some fluctuations on normal force even refining the mesh. The problem comes when I give the cylinder body an initial condition with a rotational velocity of -13rad/s . The analytical solution for the problem is -11.61rad/s. If I plot the rotational velocity I see the following curve:
I know maybe it has something to do with the friction coefficients and with applying the initial velocity on t=0seconds. So, since the analytical solution does not require any information about the friction coefficients, I would like to ask if someone knows a way to apply a velocity to the cylinder so that when it gets to the last point of the horizontal plane, it has a velocity equal to the analytical solution before start rolling from plane A to plane B.
Thanks in advance,
Javier
Answers
-
PS: I attach a picture so you can see the FE model
The cylinder has a mass of 4.24Kg , a radius of 0.05m and L= 0.2m
0 -
Can you also provide the model? There are many possible things to consider here, not just mesh refinement on the contacts. While the textbook problem is relatively trivial, using a multibody dynamics code to reproduce these results is not as easy as it appears to be at first. Contacts + friction always add a lot of numerical complexity to the solution.
0 -
One possible suggestion: Make sure you are applying not only an initial rotational velocity to the cylinder, but the equivalent translational velocity as an initial condition. If you are only applying an initial rotational velocity, the cylinder is just spinning, and not translating at t=0. Therefore some energy is lost as the cylinder starts to accelerate.
Edit: This is exactly the issue. I was able to reproduce your problem quickly on my end with a simple model. You need to specify the translational and rotational initial conditions. If you set the problem up correctly like this, you will find that you will not even need friction to solve the problem. Friction really isn't needed in the analytical solution either. Friction in contacts (or joints) should only be used when absolutely necessary to solve for the physics of a particular problem. Using friction requires knowlege of the correct friction to use, and how to apply it correctly. You will find that in most MBS problems, friction really isn't needed. Often we will add viscous damping to a model, as an approximation for friction, as it's numerically much more efficient.
0 -
Thank you very much Chris. That's true, I was very obsessed with giving the cylinder an initial rotational velocity when the solution of the analytical problem is the initial translational velocity.
I'm going to try what you just told me and see what happens. That problem is not very complex to solve analytically although the condition you have to find to solve it is not trivial (N>0 and integrate the change on rotational velocity through the transition from plane A to
. However, I knew solving it on a simulation environment was going to be tricky because of the friction and geometry discretization.
Thanks for the tip too! I didn't know applying viscous damping is more efficient. Is there any particular guideline to know how to apply a viscous damping that simulate a similar effect that the real friction force?
0 -
I tried again with your suggested solution and that's what I obtained:
<?xml version="1.0" encoding="UTF-8"?>
It seems everything is working fine, the only thing that bothers me is that initially the cylinder is contacting the plane so I don't know why I obtained this peak on the contact force curve at the beginning of the simulation as if the cylinder hits the surface.
Also, when the cylinder leaves the inclined plane it should maintain the rotational velocity because there is no friction with the air.
0 -
I would suggest investigating the integrator settings you are using. If you are using the default parameters, those are usually not sufficient when using contacts. Under simulation settings
You also need to be careful about the contact parameters. There is an entire section on best practices for contacts in our help. If you have even a slight initial penetration of the cylinder with the ramp, there will be an initial spike in forces.
FYI, there is an online class for MotionView being offered next week. I would highly recommend you sign up for it, if space is still available.
0 -
Thank you very much Chris. I'll check the integrator settings.
Let's see if they have some spots available, I'll let you know if I have more issues with the simulation.
Thank again for your time
/emoticons/default_biggrin.png' srcset='/emoticons/biggrin@2x.png 2x' title=':D' width='20' />
0