Problem with coupling resoults
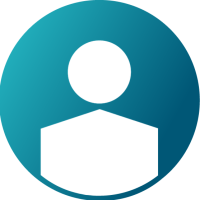
Good morning to all;
I have a problem with a cosimulation between EDEM and Hyperworks CFD.
I put you in situation. I have a venturi tube with a deposit loaded with dust particles (I have calibrated these particles myself). The problem is that when I want to do the cosimulation, the particles sometimes cross the boundaries of the flow, getting lost in space (you can see an example in the image).
Does anyone know what can be due?
In addition, I take the opportunity for another concept question. When I do the cosimulation, where exactly do I apply the scale factor that I have given to the particles? Furthermore, the particles have different shapes, and when configuring the flow material in Hyperworks I don't know how to enter the different inertia parameters for non-spherical particles.
Thank you very much and greetings
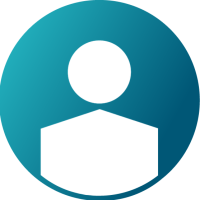
Finally the problem was a sum of errors, but your indications were very helpful.
All the best
Hi Joshua,
I would recommend trying a few 'best practice' points:
If either case doesn't run single phase it is typically easier to resolve that first before moving to multi-phase.
When running multi-phase both solutions may be stable stand-alone however the time-step ratio could be too high. Typically EDEM will run at time-steps orders of magnitude lower than AcuSolve. You don't need a 1:1 ratio as this would be computationally too expensive however it is worth considering how far a particle moves in 1 AcuSolve time-step. We would want a particle to 'exist' within a mesh cell for a number of timesteps in order to resolve the forces without too significant a change each timestep.
The geometry doesn't' have to match-up exactly and in some cases can be beneficial to model a larger domain in CFD and smaller domain in DEM, especially if the particles are restricted in where they can flow by the geometry. However if by accident the geometry is imported at different scales then this can apply artificially high forces or cause problems with stability.
For non-spherical particles you can set the aspect ratio as per this tutorial - https://2021.help.altair.com/2021.2/hwsolvers/acusolve/topics/tutorials/acu/acu_6104_intro_cfd_r.htm#acu_6104_intro_cfd_r
The inertia is calculated in EDEM via the Creator > Bulk Material > 'Particle name' > Properties tab. You can manually input the inertia or use calculate properties option for the given shape, on recieving drag forces from AcuSolve and resolving contacts and any other forces the motion will be resolved based on the particle properties set here.
Regards
Stephen