Error 312
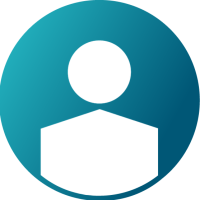

Hi,
during the second Iteration, Optistruct shows following Error Message:
ITERATION 2
*** ERROR # 312 ***
In static load case 1
the compliance is negative or large 6.051219E+09
Optimization/buckling analysis cannot be performed
due to possible rigid body mode
Objective Function (Minimize VOLUM) = 4.13553E+06 % change = -36.03
Maximum Constraint Violation % = 0.67867E+06
Design Volume Fraction = 4.95356E-01 Mass = 1.11659E+01
Subcase Compliance
1 6.051219E+09
And on the last page of the report, the same Error is shown:
A fatal error has occurred during computations:
*** ERROR # 312 ***
In static load case 1
the compliance is negative or large 6.051219E+09
Optimization/buckling analysis cannot be performed
due to possible rigid body mode
INFEASIBLE DESIGN (AT LEAST ONE CONSTRAINT VIOLATED).
Does anybody know how to avoid this Error? And what it means?
With only one Iteration during calculation, the Error does not occur!?
Thanks for your help!
Answers
-
The error may due to the presence of some rigid body modes some where in the model so kindly check the constraints or welds where rigid modes might occur or else the displacements may be too high so you may reformulate your problem to minimize compliance and put a constraint on volume fraction for say 0.3.
0 -
Hello,
as Rahul mentions, this error occurs when you have a model with insufficient constraints or a bad optimization definition. It would be probably best, if you upload your hm or *.fem model to this website or dropbox, so that we can have a closer look. You can before that check:
1) Does your model have constraints in the defined loadstep (SPC entry?) --> you need to define in your loadstep, where the model is fixed
2) Your optimization might be defined in a way that allows optiStruct to remove material between the loading and the fixed constraints. That can happen e.g. when defining an optimization with objective min. Mass and Design Constraint displacement < xx mm, when the displacement is chosen far from the load path.
Please redefine your optimization in this case in the way that Rahul told:
a) Define responses 'massfrac' and 'compliance'
/emoticons/default_cool.png' alt='B)'> Define objective = minimize compliance (meaning minimizing all displacements)
c) Define a Design Constraint 'massfrac < 0,3' (meaning that only 30% of the material can be used to achieve min. displacement)
Jan
0 -
Hello,
First of all, thanks for the fast response!
We have tried to improve our optimization like your instructions. But we still get the same error.
In the following link you will find two .hm files. The first one is the originally file. (subframe_hinterachse_Netz_entfernt_mit_eigengewicht6.02_3.hm)
And the second one is the file that we had improved. (subframe_hinterachse_beidseitige_Kraefte_mit_Diff_Kraefte_2.hm)
https://www.dropbox.com/sh/ys1qggvd4ctvnco/AABhUa333sGaV1ACRKYDq1maa?dl=0
It would be very nice if someone could have a look at the files.
We have some more questions:
- How can we adjust the range of the regulator in the ISO Menu in HyperView. We want to look for a larger range
- How can we define, that some parts of the component are not optimized. In our example we want to keep the flaps in the originally shape.
Thanks in advance!
0 -
I am unable to use the dropbox link, can you use the secure dropbox in the signature below?
In order to adjust the range of the regulator in the ISO menu, you have to first apply an ISO, so select a result type in the menu > select the components > apply.
In order to make sure some parts of the component are not optimized, always make sure the parts you do not want modified are put into one component, then make sure this component is assigned with a different property,
so when you create a topology optimization design variable, you can make sure that you select only that property which is assigned to the components you want modified.
0 -
OK, files are uploaded.
Subject: Error 312
0 -
The file called - subframe_hinterachse_beidseitige_Kraefte_mit_Diff_Kraefte_2
Runs without errors for me here on my 13.0 version of HyperWorks - Optistruct.
0 -
Hello,
it seems that in v13, the error 312 has been changed to a warning 312 (meaning the analysis will not stop but instead give you only a warning message to check your model)
When running only an analysis in OS 13, I realized that you have very, very high displacements in your model (about 0,8m of bending displacement). Probably this is due to an unmeaningful loading. Please check the loads in your model. Be aware that applying e.g. 200N to 1800 nodes meany you apply a load of 1800 x 200N = 360000 N (36 tons).
It will be easier, if you create an RBE3 element (Mesh --> Create --> 1D --> RBE3) and apply the load to the center node only. This means, the 200N will be distributed evenly amongst all RBE3 nodes. See the attached picture.
Jan
0 -
Hello again,
thanks to Rahul and Grasmannsdorf !
We have changed the load. That was the mistake:
Be aware that applying e.g. 200N to 1800 nodes meany you apply a load of 1800 x 200N = 360000 N (36 tons).And we also used the RBE3 element.
After all we got the results we wanted.
Thanks
0 -
Hi there,
I got the same error-message in my optimization.
I already tried many of configurations. Probably the problem is in the RBE2 which induces the forces. The displacement gets huge und optimization stops because of to large compliance.
I know, that its recommended to use RBE3, but for the usecase I'm investigating, it would be more realistic to use a RBE2 (pole impact, so no relativ movement between the connected nodes in x-direction). Nevertheless I also tried with RBE3 but it still finds no feasible design in 200 iterations (but no error 312). It also works, if I add another constraint on the independent node in all directions but x, but the results are not useful then.
I also tried with minimize compliance and massfrac as constraint - it works with exactly the same load case and the results look very good.
But while the literature research I read, that structure could be different with minimize mass as objective and I'd like to verify this.
So could anybody tell me, where's the mistake in my attached loadcase-setup? I get this warning message in output file:
*** WARNING # 1662
Constraint reduced AUTOSPC DOF(s) listed below usually are related
to a modeling error. Please review the model.
GRID 279805 DOF 6
Number of constraint reduced AUTOSPC DOFs = 1
List of Auto-SPC d.o.f.s for loadcase 33
Total number of Auto-SPC d.o.f.s = 7
------------------------------
Grid No. Component
------------------------------
279805 2 3 4 6
279806 2 3 4
------------------------------
Would be very thankful for any help cause I'm running out of time for my master thesis.
Best regards,
Felix
0 -
Hi,
I will check the file and update you soon.
0 -
Hi @FBeck
Can you try this: Minimize (total/regional) volume/mass fraction With constrained displacements
Instead of having mass, use the mass fraction as the response.
0 -
thanks for your quick Reply! Thats another helpful and interesting advice!
I think I found the Problem though. I only constrained the outer Elements in x-displacement. Because of this, the other Elements were allowed to have this huge displacement and that probably lead to the large compliance. As I constrained all Elements in x-direction now, optimization converged and the results look good.
There's only one Thing I'm still not happy with: As shown below there's a gap in it. At the Moment Elements of the front side go through the rear side.
How could I prevent this? Could I create Kind of a selfcontact (one component)?
Thanks a lot!
0 -
Hi,
There's only one Thing I'm still not happy with: As shown below there's a gap in it. At the Moment Elements of the front side go through the rear side.
How could I prevent this? Could I create Kind of a selfcontact (one component)?
One way is to move a layer of elements to non-design space to avoid the scenario. Self-contact may not work with a linear static subcase.
0 -
Hi,
I have a part where I just want to optimize minimum mass with a maximum node displacement of 2 mm. I have define a dconstraint of static displacement. The problem is that some areas of my part are not going to suffer any loads, so during the Free Size Optimization Altair deletes the plies on those areas (it doesn't delete them, it just gives them a really low thickness value, 0.1% of the initial one). I need my part to have the same shape as the surface that I am importing as a geometry, I just want OptiStruct to give me the optimum ply configuration. How can I assure that? Besides, the optimization is giving me a #312 error when I apply a pressure load, although it doesn't show that error when carrying out a static analysis. What can be the cause of it?
Thanks in advance
Attached you may find some pictures of what the geometry looks like. The forces and moments are applied in a remote point and transferred to the surfaces where they act through some rigid bars (first picture) and the pressure acts on almost all the surface (second picture).
0 -
Altair Forum User said:
Hi,
I have a part where I just want to optimize minimum mass with a maximum node displacement of 2 mm. I have define a dconstraint of static displacement. The problem is that some areas of my part are not going to suffer any loads, so during the Free Size Optimization Altair deletes the plies on those areas (it doesn't delete them, it just gives them a really low thickness value, 0.1% of the initial one). I need my part to have the same shape as the surface that I am importing as a geometry, I just want OptiStruct to give me the optimum ply configuration. How can I assure that? Besides, the optimization is giving me a #312 error when I apply a pressure load, although it doesn't show that error when carrying out a static analysis. What can be the cause of it?
Thanks in advance
Attached you may find some pictures of what the geometry looks like. The forces and moments are applied in a remote point and transferred to the surfaces where they act through some rigid bars (first picture) and the pressure acts on almost all the surface (second picture).
0 -
-
Hello all, I was working on buckling load case but the value for that was in the range 0.05 or 0.06 the factors in post processing.... Can anyone suggest the reason for.that. Thank you0