Bearing loads
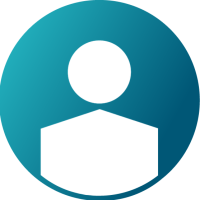

I'm looking to apply a bearing load to a cylindrical face, eg force on conrod from bearings. Now the part will only undergo compressive stresses, with a distribution from max at the bottom to zero at the sides, since the bearings can't pull on the bores, only push.
Does anyone know how I can model this?
Cheers
Answers
-
Hi, it depends on how you are planning to model your assembly - i.e. are you modeling only the target shaft, on whose cylindrical face you are planning to give the bearing load? Or, are you modeling a whole large assembly which includes the target shaft, bearings model, source shaft and other components & that you are giving the force or moment to the source shaft and want to check the effect/stresses on the target shaft?
In the former case where you are simply modeling the target shaft and you know the force applied by the bearing on it's cylindrical face, mesh the shaft while ensuring a uniform symmetrical mesh is applied on the bearing-contact face. At the bottom-most node of this face, apply the max force & at the end nodes apply zero force (or no force at all). For the remaining nodes in-between them, calculate a parabolic curve y=A*(x^2) with force on y-axis and node position on x-axis with which for each of the in-between nodes you will get the force values. Apply these forces at those respective nodes. Note that the direction of the forces must be normal to the cylindrical face at whichever node they are applied to.
Check this article for reference: http://help.solidworks.com/2010/english/SolidWorks/cworks/LegacyHelp/Simulation/LoadsRestraints/Bearing_Loads.htm
In the latter case of a large assembly, where you are modelling not only the target shaft - but also the bearing, source shaft and other components, you need to model the bearing with Rod elements. To do so, first delete the bearing's 3D-model from the assembly. Then while meshing, make sure the cylindrical contact faces of both the source as well as target shaft have uniform, symmetrical & MATCHING meshes. Then, connect each of the matching nodes on the source and target faces with Rod elements (Go to 1D panel > rods, choose element type as CROD). Then, you can apply the forces at respective assembly locations & submit the FE model for analysis. The Bearing effect will be automatically simulated by the Rod elements & you can check the stresses or forces on the target shaft as necessary.
0 -
Awesome, thanks for the reply Sprash, that's really helpful.
I'm generally only modelling the target shaft (hole in this case), so the first method should do.
Cheers
0 -
Yes I like ^^
0 -
Create a cylindrical coordinate system at the center of the bearing and with the R axis pointed in the direction of the load. Then create an force equation:
F = Load * cos(T)
Basically, load decreases with angle away from the R axis.
There are numerous studies for what this equation should be with higher order terms but cosine is a reasonable approximation.
0