Query about Geometry Cleanup and Meshing
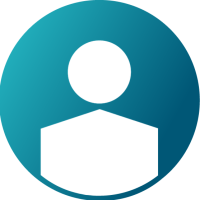

I am using OptiStruct, HyperMesh 13.0. I want to do static analysis of a bracket which joined with circular pipe, before analysis i am facing geometry cleanup and also meshing, i don't have any idea about geometry cleanup, i studied and watched tutorial about that but in my problem i don't know how to do this..kindly help me out regard this matter, Thanks.
Answers
-
Don't try 'autocleanup'. Do that manually so you can learn more.
0 -
Hi,
With the geometry cleanup process we are making the model geometrically continuous, that is all the gaps in between them are closed and thereby a geometry connectivity is created with the edge edit tools. The connectivity of surface edges constitutes the geometric topology.
The perimeter of a surface is defined by edges. There are four types of surface edges:
•Free edges
•Shared edges
•Suppressed edges
•Non-manifold edges
Free edges are colored in red and they appear between two adjacent surfaces indicate the existence of a gap between the two surfaces which need to closed.
Non-manifold edges are colored yellow and they typically occur at 'T' intersections between surfaces or when 2 or more duplicate surfaces exist. Duplicate surfaces need to be deleted.
Shared edges are colored green. When the edge between two surfaces is a shared edge, there is no gap or overlap between the two surfaces - they are geometrically continuous.
Suppressed edges are colored blue.Like a shared edge, a suppressed edge indicates geometric continuity between two surfaces.
With the geometry cleanup we normally clear only the free and non manifold edges to make them shared edges, that is geometrically continuous. Since your model don't have any free edges and non-manifold edges you can go ahead with meshing.
0 -
Altair Forum User said:
Don't try 'autocleanup'. Do that manually so you can learn more.
Thanks bro, Yes you are right. I want to learn more...
0 -
Altair Forum User said:
Hi,
With the geometry cleanup process we are making the model geometrically continuous, that is all the gaps in between them are closed and thereby a geometry connectivity is created with the edge edit tools. The connectivity of surface edges constitutes the geometric topology.
The perimeter of a surface is defined by edges. There are four types of surface edges:
•Free edges
•Shared edges
•Suppressed edges
•Non-manifold edges
Free edges are colored in red and they appear between two adjacent surfaces indicate the existence of a gap between the two surfaces which need to closed.
Non-manifold edges are colored yellow and they typically occur at 'T' intersections between surfaces or when 2 or more duplicate surfaces exist. Duplicate surfaces need to be deleted.
Shared edges are colored green. When the edge between two surfaces is a shared edge, there is no gap or overlap between the two surfaces - they are geometrically continuous.
Suppressed edges are colored blue.Like a shared edge, a suppressed edge indicates geometric continuity between two surfaces.
With the geometry cleanup we normally clear only the free and non manifold edges to make them shared edges, that is geometrically continuous. Since your model don't have any free edges and non-manifold edges you can go ahead with meshing.
Thank you so much dear, now i have done meshing so you can check in attahed file. i have done 3D volume tetra mesh by selecting the all solids after that i got a message 2 failed you can check in mesh1 picture and some of elements quality problem like aspect ratio, skew, tet col, lengths, min angle, cell squish. etc those elements are not good. so, now what should i do?
0 -
Hi,
To improve the mesh quality either user has to perform a remesh or has to manually perform the translation of nodes.
Please go through http://www.altairuniversity.com/wp-content/uploads/2014/02/elemquality.pdf which describes about tetra elements quality parameters.
And I recommend you to go through this video which shows tetrameshing process with quality checking and improving: https://www.youtube.com/watch?v=oF7td7PbpoQ
0 -
Altair Forum User said:
Hi,
To improve the mesh quality either user has to perform a remesh or has to manually perform the translation of nodes.
I'm attaching a document on tetramesh quality checking. Please go through the same.
And I recommend you to go through this video which shows tetrameshing process with quality checking and improving: https://www.youtube.com/watch?v=oF7td7PbpoQ
I have watched this video many times and also learnt from this video, i have shown in above picture and just follow the 3d meshing procedure but still my meshing is not good.
0 -
-
Hi Waqas,
Looks like property is missing on elements. Please check and update
0 -
Altair Forum User said:
Hi,
To improve the mesh quality either user has to perform a remesh or has to manually perform the translation of nodes.
I'm attaching a document on tetramesh quality checking. Please go through the same.
And I recommend you to go through this video which shows tetrameshing process with quality checking and improving: https://www.youtube.com/watch?v=oF7td7PbpoQ
Altair Forum User said:Hi Waqas,
Looks like property is missing on elements. Please check and update
I am facing another problem i am doing simple analysis of 3D circular pipe you can show in the pic in the final result i am getting this kind of errors as mentioned in the picture.
and....do you have any idea about solidthinking inspire what is the difference between hypermesh and solidthinking inspire analsysis?
0 -
Hi,
There are some shell elements in the model, which you may have created for solid mapping. The error shows that those elements are missing property.
Please delete the shell elements in the model and try running.
0 -
Altair Forum User said:
Hi Waqas,
Looks like property is missing on elements. Please check and update
Altair Forum User said:Hi,
There are some shell elements in the model, which you may have created for solid mapping. The error shows that those elements are missing property.
Please delete the shell elements in the model and try running.
I used solid as a enclosed volume in 3D Volume tetra Mesh. but meshing is still lots of problem as shown in below figure. kindly tell me whats wrong with this?
<?xml version="1.0" encoding="UTF-8"?>
0 -
Hi,
This seems to be only a graphical issue. You can just hide the surface from the model tree and review the elements in the model.
0 -
Altair Forum User said:
Hi,
This seems to be only a graphical issue. You can just hide the surface from the model tree and review the elements in the model.
after my simulation work it showing that.....??? what does it mean?
0 -
Hi,
The above image seems to be graphical issue. But the error is due to the mesh quality. You may need to improve mesh quality in the model.
Keep CHECKEL to NO (Analysis>Control Cards>PARAM>CHECKEL to NO) and try running the analysis.
0 -
Altair Forum User said:
Hi,
The above image seems to be graphical issue. But the error is due to the mesh quality. You may need to improve mesh quality in the model.
Keep CHECKEL to NO (Analysis>Control Cards>PARAM>CHECKEL to NO) and try running the analysis.
If we will do that so it will not affect on our final analysis? another thing is that if quality of meshing is not good? what will happen on the analysis?
0 -
Hi,
PARAM>CHECKEL to NO may affect your results. But if the poor quality elements are not at critical regions I think you can go ahead.
A low quality mesh lowers the accuracy of FEM results. In the formulation of finite elements a local parametric coordinate system is assumed for each element type and how well the physical coordinate systems, both element and global, match the parametric dictates element quality.However, there will be a point of diminishing return if you try too hard to get every element within the acceptance criteria. Your judgment is your only guide in those cases. In general, poor element shapes can cause convergence issues in analyses and can produce inaccurate results, especially when they’re at critical locations.
0 -
Altair Forum User said:
Hi,
PARAM>CHECKEL to NO may affect your results. But if the poor quality elements are not at critical regions I think you can go ahead.
A low quality mesh lowers the accuracy of FEM results. In the formulation of finite elements a local parametric coordinate system is assumed for each element type and how well the physical coordinate systems, both element and global, match the parametric dictates element quality.However, there will be a point of diminishing return if you try too hard to get every element within the acceptance criteria. Your judgment is your only guide in those cases. In general, poor element shapes can cause convergence issues in analyses and can produce inaccurate results, especially when they’re at critical locations.
Hi George,
i am showing my analysis result could you tell me further about that... i have material type is SS, E=204999.9 MPa, Nu=029, density = 7.8 kg/mm3, Yield strrenght is 283 MPa. I used in constraint type 6 dof, and each load is 200N. According to result von misses is 263 but deflection is too much...kindly tell me about how to verify our result and also how to check factory of safety.
<?xml version="1.0" encoding="UTF-8"?>
0 -
Hi,
I suggest you to consult with your University professors on results validation.
0 -
Check your mesh. Check your assembly.
0 -
Altair Forum User said:
Hi,
This seems to be only a graphical issue. You can just hide the surface from the model tree and review the elements in the model.
in the below meshing part picture, the nodes are not connected to the other part so what does it means? the two parts are not joined eachother?
0 -
Altair Forum User said:
Hi,
I suggest you to consult with your University professors on results validation.
dear friend, my prof. said to me search yourself thats why i asked to you. Kindly, i am requesting to you help me out regard this.
/emoticons/default_smile.png' srcset='/emoticons/smile@2x.png 2x' title=':)' width='20' />
0 -
Altair Forum User said:
Hi,
If that is a continuous component it has to be connected. Try to get a nodal connectivity or use RBEs
0 -
Altair Forum User said:
Hi,
If that is a continuous component it has to be connected. Try to get a nodal connectivity or use RBEs
my component is like that in the picture. you mean the nodes should be connected to the other parts? if i use to connect the nodes the shape of whole meshing component is changed.
0 -
Hi,
Not sure where exactly you have the problem with mesh in your model. If possible, can you share the model file?
0 -
Altair Forum User said:
Hi,
If that is a continuous component it has to be connected. Try to get a nodal connectivity or use RBEs
OK.
0 -
Hi WikiJoy,
There are modelling mistakes in your model.
1) Nodes are not connected
2) You may have to use tie contact or RBEs wherever it is necessary .
Run a normal modes analysis to check the connectivity or select one element (say in mask panel) and do by attached. You will get to know which elements are isolated.
0 -
Altair Forum User said:
Hi WikiJoy,
There are modelling mistakes in your model.
1) Nodes are not connected
2) You may have to use tie contact or RBEs wherever it is necessary .
Run a normal modes analysis to check the connectivity or select one element (say in mask panel) and do by attached. You will get to know which elements are isolated.
Could you tell me how to start my meshing from starting?, i did myself but the reuslt you know...
1st step i did just checked the free and non-manifold edges, in visualization option there is no these kind of edges found in my model and then i did volume tetra mesh by selecting one by one surface.
and tell me how to make one surface in hpermesh if we have a different solids and surfaces?
0 -
Altair Forum User said:
Hi WikiJoy,
There are modelling mistakes in your model.
1) Nodes are not connected
2) You may have to use tie contact or RBEs wherever it is necessary .
Run a normal modes analysis to check the connectivity or select one element (say in mask panel) and do by attached. You will get to know which elements are isolated.
Could you tell me how to start my meshing from starting?, i did myself but the reuslt you know...
1st step i did just checked the free and non-manifold edges, in visualization option there is no these kind of edges found in my model and then i did volume tetra mesh by selecting one by one surface.
and tell me how to make one surface in hpermesh if we have a different solids and surfaces?
0 -
-
Altair Forum User said:
Thank you so much. Got it.
0