contact problems between two components
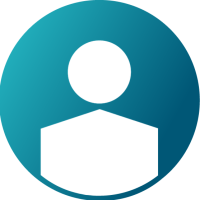

Hello,
I have a problem by creating a contact surface between two components.
I wanted to realize a stick contact, but only a few nodes interact, so at these nodes massive peak of stress appears.
I tried to change change the parameters, so i reduced the mesh-size and tried a friction-contact with a high coefficient between the two parts. The result was the same.
After this I changed the parameters fo Freeze and MOrient = Normal.
The result was way better, but a peak with high stress appeared at the end of the contact surface.
Moreover I tried to expand the contact surface.
You can see the results in the pictures, which I attached to this post.
Also I added the .hm and the .h3d file.
Can you tell me, where i made a mistake or how I can fix the problem?
Thank you very much in advance for your help.
Best regards
M. Herrmann
Hello,
the issue in your model seems to be, that you run a linear - static analysis.
*** INFORMATION # 2406
There exist gap/contact elements and linear analysis SUBCASE(s).
For linear SUBCASE, the gap/contact behavior depends on the
initial open/closed status and does not change.
For Stick or Slide contact, you need to define a 'non-linear quasi static' analysis however, as the contacts need to be iterated, so that a realistic behaviour occurs. The solution would be either a freeze contact, which will close ALL connected nodes. Then the analysis will be linear again, however you don't have a 'real' contact (which would mean only compression loads will be transferred) but instead full connection between the parts (which means compression AND tension will be transferred).
I think the high stresses in case of FREEZE contact are realistic, as the end of the contact surface is the area of lowest stiffness in the connection --> highest strain and stress there makes sense to me.
Or else, if you want to run nolinear + contact, you will need to define a NLPARM entry (as a loadcollector) and reference it in a loadstep of type 'non-linear' (NLPARM = ID of the previously defined entry). Please note the difference between the different contact types:
STICK - will close all nodes when they get in contact and NOT reopen them in case the loadsituation changes. Imagine it as two surfaces with glue on it, which stick together once they get in contact
SLIDE - will close all nodes when they get in contact. However the surface can still 'slide' on each other and are allowed to lose contact if the load changes
FREEZE - will act like 'stick', but with ALL the surfaces glued together right from the start.
Please have a look at the chapter 'non-linear analysis' of our free E-Book 'Practical Aspects of Finite Element Analysis'. There are some good pictures on the different contacts and how to set up a non-linear contact analysis. The book can be requested here:
http://www.altairuniversity.com/free-study-guide-book/
Best Regards
Jan