High Compressions in tooth contact of two gears
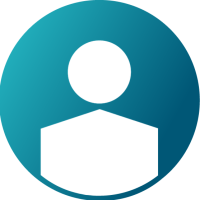
Hello everyone,
i am doing gearbox simulations with two gears with NanoFluidX. Now i am troubeling with the results of my simulations.
In the tooth contact of the two gears it comes to local high pressures and in cause to local high velocitys during the simulation. By this is caused an instability around the tooth contact which blows away all the particles, as you can see (the gears are not visualised, in the attachment you can see a section view of the gearbox).
<?xml version="1.0" encoding="UTF-8"?>
I think this appears because the particles are compressed very high or is there another reason?
Is it possible to cut of pressures above a certain value to eliminate these compressions?
I have also attachted the .cfg file of my simulation.
Thanks a lot!!
Answers
-
You are correct in that as the gear teeth come together, the fluid particles feel increased pressure and move away from those areas. It will typically move laterally away from the contact areas. With the typical resolution (dx) in the mm range - looks like 0.7 mm in your case - nFX will not capture the flow between the teeth themselves, as this is of a much smaller length scale. There should also be a small number of these hot/fast particles compared to the total. You should still be able to see fluid on the left side of the gear contact area, but it would most likely then be air. Do you see the air phase there instead?
You can see if reducing the time step makes a difference. There are a few ways you could do this:
1. Increase ref_vel_factor
2. Decrease dt_factor
3. Find the computed reference velocity in the output file itself, then set ref_vel to a higher value than that in the 'domain' section
4. Find the computed time step in the output file, and specify it manually to a lower value - this is probably the least desirable manner...
It looks like there is not much clearance between the gears and the housing in the screenshot provided. If you look from the other direction, is the housing also very close to the gears? If yes, where the gears are very tight to the housing on all sides, it may take a fairly low time step to get good stability as there is not much volume for the fluids to stabilize much.
0 -
Thanks for your reply! The effect on the air particles is smaller than on the oil but they are pushed away as well.
And the distance between the hosuing and the gear is about 6mm on both sides. I think that should be big enough. I will try to reduce timestep to get the simulation more stable.
0 -
I would expect in this case that the reference velocity based purely on the rotating bodies (X 1.5 by default) is not enough due to likely large regions of acceleration with the walls so close. If you go really high, say ref_vel_factor 3.0 instead of default 1.5, how much of a difference does it make?
0 -
This will reduce the time step to the half. But then also lower accelerations might not be solved anymore. I think another solution might be to reduce the width of the gears. They are by now 25mm.
0 -
i now tried with ref_vel_factor 3, but the simulation result is still the same with the instable behaviour.
0 -
Does the result get any better at all? If you look at both air and oil particles together - does the void decrease in size? What if you increase ref_vel_factor even more - say to 6.0? Is there additional decrease in the size of the 'void'?
Are many fluid particles being removed - 'escaping' through the walls and/or moving inside the gears? The fluid particles 'feel' increased pressure due to the teeth being close together. Sometimes they get moving so fast that they pass through the walls - especially with not much space between the tooth contact region and the outer walls.
You mentioned 6 mm between the gears and the housing (I'm assuming from the larger faces of the gears). How much space between the gear teeth and the 'curved' housing walls? What is the distance across a tooth tip?
How many layers of particles do you have for the housing and the gears themselves?
0 -
Hi all,
I was following your discussion with interest, as I am approaching nanoFluidX.
Is it somehow possible to download the .cfg file posted by Linux34 at the beginning? It currently does not allow me to.
Thanks a lot,
Mattia
0 -
Mattia Setti said:
Hi all,
I was following your discussion with interest, as I am approaching nanoFluidX.
Is it somehow possible to download the .cfg file posted by Linux34 at the beginning? It currently does not allow me to.
Thanks a lot,
Mattia
I expect the attachments are removed after a certain length of time, so there's likely no way to retrieve that file.
0