Request for some tips in honeycomb meshing and attachment with carbon layers
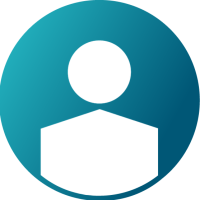

Hi All,
FYI, the model is a sandwich panel (with aluminium honeycomb at center and one layer of carbon on each side- top and bottom) used in monocoque. Well, I am stuck at meshing of honeycomb and unable to get consistency in results.
While trying on the actual cut sample (LxW- 368mm x 176mm), I got 'volume analysis failed' and 'temp_2d_for_tetra' for many a times and so I thought I should try on a small pattern (70mmx35mm). After trying on a small pattern, the carbon layers are not attached while viewing in HyperView, i.e. honeycomb deforms individually and carbon layers deform separately at higher frequencies. I created the assembly in SolidWorks ('mate' in assembly file) at first, it gave the results as mentioned above (carbon layers not attached with honeycomb).
Next I created lines on outer edges of honeycomb in HyperMesh (to develop carbon layer), assigned thickness (of carbon) and meshed it; but in both cases, the honeycomb is not attached to carbon (while viewing '.op2' file in HyperView).
Can you please help me out with this? Much appreciated.
Thanking You.
Kind Regards,
Shreerang
Answers
-
Hi,
Could you share us screen shot of model and results?
Regards
Rahul R
0 -
Hi Rahul,
Thank you for your reply. Kindly let me know what result file do you want me to share. I have attached a screenshot of HyperMesh Model and two different images (at different frequencies) from HyperView.
Also, FYI, the card images and element size used so far in HyperMesh might not be the best (suitable) but I am not able to figure out the reason behind the layers not being attached with each other.
Thanks and Regards,
Shreerang
file:///E:/three_layers.PNG
file:///E:/rupture_1_.PNG
file:///E:/rupture.PNG
0 -
Hi Rahul,
Referred to my previous reply, I tried attaching SolidWorks (assembly) file for your reference but somehow it did not get uploaded. Kindly let me know if there is any other way to upload here. I tried with 'More Reply Options', etc.
Thank You.
0 -
Seems like your trying to mesh the structure with tetras, am i right? I think it would be better to use Shells to begin with..
0 -
Hi there,
Well, when I was importing the whole pattern from SolidWorks (IGS file) in HyperMesh, I could select it as solid using 3D--> tetramesh--> Volume Tetra and used to get 'volume analysis failed'. I made some changes to honeycomb in SolidWorks and then to my surprise, later on I could never select it as solid (I might have made a mistake in SolidWorks as I started learning it because of this structure/project). Hence, I created a small pattern and started trying with 2D automesh. I started trying with quads, mixed and trias so as to keep it simple and just to make sure it gives me output once.
The picture you see is using 2D itself. Please let me know if you would like to know any further details. I am not able to understand the reason behind it not being attached to the carbon layer.
Thanks and Regards,
Shreerang
0 -
Sorry, but i can't view any pictures, the links you provided don't work (they appear as plain text)
As for the connection between honeycomb and the carbon layer, you have to ensure to actually model some type of connection. There are several options available, e. g. merging nodes, tied contact, using connectors ...
0 -
Thanks for your reply. I think I did not attach the images properly, my bad. I have tried to attached hereby. Kindly see attached and confirm.
Well, I used equivalence option to make sure of the connection. Do you think it is a recommended option? Please let me know.
Thank You.<?xml version="1.0" encoding="UTF-8"?>
0 -
So, you are using SHELL-Elements for both, Carbon and HC?
Could u send a Picture were one can see the mesh of the carbon? I think you are using a pretty coarse mesh for the HC.
You should use the that type of Connection which best fits your desired output, depending on the desired detail, so to say. For instance, if your not interested in failure or deflectional behaviour of a bonding layer (or whatever), then i would choose a tied contact (in optistruct available via PCONT- or TIED-Keywords. TIE works well, i recently figured).
0 -
I really appreciate your concern.
Here is the image of mesh of carbon (used quads for simplicity). I am using coarse mesh, element size as 4, so as to save the time using Nastran. Previously when it gave me output for few trials, I had used lets element size 1 (which is still not fine mesh).
I have got a know-how of using equivalence/free edges wherein I go to a certain limit else the structure collapses and I get this error
'USER FATAL MESSAGE 4297 (EQD4D)
QUAD4 ELEMENT WITH ID =7430HAS AN INTERIOR ANGLE POSSIBLY GREATER THAN OR EQUAL 180 DEGREES.'Can you please throw some light on features/options I can use if I want to solve with SOL 103 and SOL 111 (in Nastran)? Do you think the option 'contactsurfs' in Analysis section will be of any help in my case?Thank you.0 -
Hi,
I am not really sure about NASTRAN, but my modelling approach will be:
If the mesh size is same, I would equivalence the nodes of different components and this works well with vibration analysis. Since contacts are non linear this is not recommended.
You can go with TIE contact as florian said.
0 -
Hi Prakash,
Thank you for your reply. I am not familiar with 'TIE' contact feature. Can you please share any article or specific link that might help? Also, by any chance, do you want me to share the '.hm' file so as to find out my mistakes or make corrections?
I am asking for the small pattern (images shared in my previous replies) because I believe the large/actual pattern that I am using for experiments will take a long time to get solved. I am getting 'volume analysis failed' or 'temp_for_2d_tetra' error repeatedly for honeycomb in the large pattern which is of no concern at this stage. Once I solve the connection issue in the small pattern, I will move to the large pattern.
A word from your end will be highly appreciated.
Thanks and Regards,
Shreerang
0 -
Hi,
You can look up the TIE Keyword in the Optistruct Helpfile.
What exactly do you mean by 'Large/small pattern', are there differences in the element size?
0