Localised re-meshing due to geometry changes
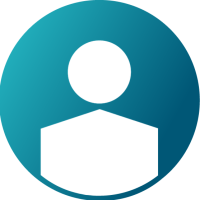

Hello. Can anyone offer any advice about localised solid (or shell) remeshing to account for geometry changes? By this I mean the following - we build an assembly model using parts created in Solidworks, which is then meshed (usually a combination of shell and solid elements). We usually need to make changes to the model which can, in the simplest case, be a hole in a part. Currently we make the hole in the solid, then remesh the whole part from scratch and this causes the remaining elements to lose connectivity across the boundaries with other parts, at connections to rigids, and at loads. Therefore, we end up (usually) having to remesh the whole assembly and reconnecting all the various parts which can be extremely time consuming just for a small modification. Ideally, we would want to be able to remove a region of elements around the modified geometry, and then remesh that area with the new elements connecting to the existing elements and also taking account of the geometry change. Is this something possible to achieve?
Answers
-
Hi,
We have some utilities in Hypermesh to create hole on FE and then create surface using FE model.Yes if model is complex and have connections it takes time to get desired mesh.
If you have some requirements like hole diameter change, fillet radius change, length change , curvature change or adding ribs on solid geometry it can possible through Hypermesh morphing Technique.
We have one more tool name Simlab which have some options to modify mesh with geometry changes.
If possible please share the screenshot of model where you want to make changes.
Regards
Rahul R
0 -
Altair Forum User said:
Hello. Can anyone offer any advice about localised solid (or shell) remeshing to account for geometry changes? By this I mean the following - we build an assembly model using parts created in Solidworks, which is then meshed (usually a combination of shell and solid elements). We usually need to make changes to the model which can, in the simplest case, be a hole in a part. Currently we make the hole in the solid, then remesh the whole part from scratch and this causes the remaining elements to lose connectivity across the boundaries with other parts, at connections to rigids, and at loads. Therefore, we end up (usually) having to remesh the whole assembly and reconnecting all the various parts which can be extremely time consuming just for a small modification. Ideally, we would want to be able to remove a region of elements around the modified geometry, and then remesh that area with the new elements connecting to the existing elements and also taking account of the geometry change. Is this something possible to achieve?
I have a hint for you do not need to mesh and connect again when changing geometry of a part, that you make a sub-boundary within your part which isolate modified zone from fixed zone (connection zone), similar to when we handle design and non-design volume of optimization process.
If you have just a small modification on geometry, it is easy to make such modification on mesh
0