Modeling of composite material interface
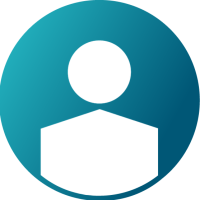

Hi,
I must model a tensile sample of composite material which consist of 3 layers of aluminium and 2 layers of fiberglass and each layer is linked by an adhesive. My problem is to model interfaces between layers, I have been advised to use gap elements to do it. Thus, on my geometry, even if layers are actually in contact, I let a small distance between them so that when I do my 2D-meshing the software does not consider them as one body and generate common grids between the two. Then I generated gap elements with the 'nodes-elems' option, it creates gaps between the nodes of each mesh and also 1D-elements on 2D-elements I selected. These gaps are stocked in a new component with a PGAP property where I set U0=0.0 (initial gap opening); KA_opts selected option : auto; and MU1_opts selected option : Stick.
The analysis I want to do is about a tensile test so I fixed one extremity of the sample and I applied a force along y-direction on the other. When I run the solver and observe results on Hyperview, these are not satisfying : it seems that gaps are useless and I obtain the exact same results when I delete them completely, all layers react independently from each other.
As I did my analysis without a huge number of elements, I tried to redefine gaps using the 'node-node' option and link all the nodes with each other, but the results are even worse : there are huge displacement along z-direction (near 30mm with a sample length of 200mm) while the force is along y-direction, plus displacement along x-direction is not consistent either. However gaps seem to keep layers stuck with each other.
Could you tell me if gap elements are really adapted to my case please. And what do I have to do to implement them well.
Thank you
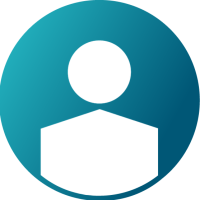

Hi Prakash,
I changed the stiffness, instead of KA=AUTO I put KA=106.E.h with E=210000MPa (steel's elastic modulus) and h=0.01mm (size of gap element) i.e. KA=210.107.
The results are exactly the same : gaps still seem to be useless.
I also tried to put KA=HARD instead of KA=AUTO, and I set KT=AUTO (transverse stiffness) as equal ...
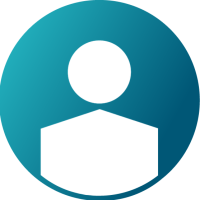

Thomas,
how the Gap elements are oriented?
Can you share the model?
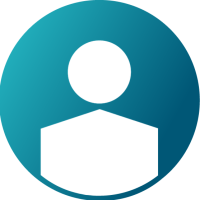

Yes of course, I attach it to the message. I didn't define a coordinate system at the beginning as I think gaps should be well oriented because of the space I let between layers, however I also tried to specify a coordinate system for gaps : I defined a new one with x-axis pointing from the layer where I selected the nodes towards the one where I selected elements, it has no effect ...
I use the solver OptiStruct.
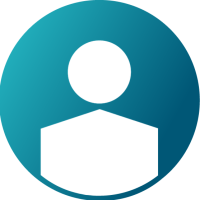
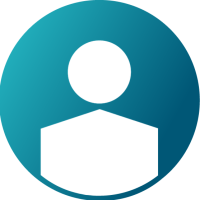

Hi Thomas,
I used your model as it is. without any changes I submitted for analysis.
Here are the displacement results in Z direction.
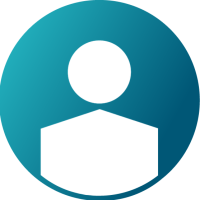

I gave you my first model where I defined gaps with the 'nodes-elements' option because if I want to increase the number of elements later it is the only possible way. The problem is that layers react totally indepently from each other and I get the same results if I run calculation on isolated layers. Here displacement on z-axis could be consistent as it shows the contraction of layers due to the tensile force, however on y-axis we can see that displacement of composite layers are much bigger than aluminium layers while they should be stuck and have displacement quiet similar.
sorry if I was not clear enough in my previous messages.
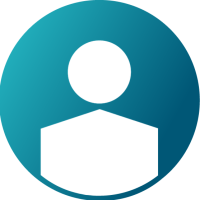

Hi,
I have been told using gap elements to produce contact between parts is becoming obsolete day by day, thus I used the contact algorithms (FREEZE represents the glue) after having created contact surfaces and interfaces.It provides promising results however there still remain problems:
First there are still annoying displacement along z-axis even if this time they are quite small, this seems to be due to an implicit bending force created by the load but I do not see why this is happening. I corrected this problem by setting a huge bending stiffness in my shell elements but I don't know if it is a valid method ...
Then, I have experimental results to validate the model, however these do not match at all with what I get with hypermesh.
I attach to this message my new model and a document detailing how I made it and observations on it. If you had any idea to modify this model so as to get closer to experimental results I would be grateful.
Thank you,
Thomas
ps: I am sure of the method I use to plot stress-strain curve as I already did it successfully with individual layers of each material
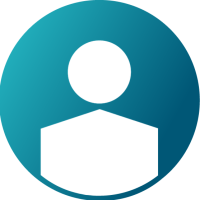

Actually I found out that results obtained match with theory, however I still have to get closer from experimental results, I tried to modify the interface stiffness but as you can see as soon as I do that layers do not stay bonded together while there still is FREEZE as contact type.
Hi Thomas,
Can you provide a stiffness to gap elements and check?
assume steel as E for gap element stiffness.