New design, determining preliminary rough geometry of a part to generate a design space for topology optimization in Inspire?
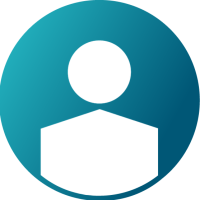

Hi all,
I am a student learning Mechanical Design. I would like to use Topology Optimization early in my design process. My problem is mainly how to determine a design space when you start from nothing. Indeed, it is quite easier when you use Topology Optimization for re-designing a product: you can take the geometry of the past product (to be re-designed), removing some features and building an envelope of the past product which you can use as a design space. But when you “start from a blank page”, designing a totally new (innovative) mechanical component, the question I ask myself is how to estimate a good preliminary (rough) design space? I think maybe to find an answer to this question it is necessary to understand the “traditional” embodiment design phase (preliminary design phase) in the mechanical design process. That is why I am writing to you today hoping you will be able to give me some advices, references to book/publications, or maybe some lines of thought so I can further my studies.
I found the least practical learning materials with methodologies (or guidelines) about the preliminary design process at the assembly and part level (structures and mechanisms). I am particularly looking for methodologies (or guidelines) for configuration design and shape/form design.
By “configuration design” I think to:
* the synthesis of the architecture of the mechanical product (structure or mechanism),
* the arrangement of the individual components,
* the determination of interfaces (when to decide for an interface? where there will be interfaces? what they will look like? preliminary sizing of connections? etc…),
* the space allocation (volume, envelope, …) for each component and weight allocation also. Understanding how (System) Engineers/Architects allocate space for each mechanical part could help me a lot for determining a preliminary design space.
By “shape/form design”, I mean determining a rough preliminary geometry/topology (synthesis) of a mechanical part from the expected loads and all requirements (functional, interfaces, etc.). How was this done when we didn’t have topology optimization technique?
I think David G. Ullman in his book The Mechanical Design Process provides us with an interesting breakdown for “Form Generation” process (part of the embodiment design): “understanding Constraints and developing Configuration, Connections and components”.
I am looking since a long time for a case study which would present the design of a mechanical system from preliminary hand sketches to final design, showing all the iterations in details done on the digital mock-up from the first CAD models to final models. I think it would be very instructive to understand the mechanical design process.
I have also studied Systems Engineering a little, and I don’t really understand why it seems one stops the systems engineering process/engine at the sub-system level or for example at the component level. Can’t a mechanical component be seen as a system itself? Actually, what I am looking for are methodologies (or methods, processes, guidelines, etc…) for what could be called “mechanical(or mechatronical) (sub-)systems engineering”. For example, Functional analysis is widely taught in mechanical design courses here in France, but there is a big gap between functional analysis, functional architecture and mechanical architecture. For now, it seems nobody has been able to write methodologies (or guidelines) which would address that issue (is that even possible…?).
I lack insight and hindsight on these subjects but I hope my questions are still comprehensible.
Here is a short list of the learning materials I own on the subject:
* The Mechanical Design Process (Book) by David G. Ullman. Interesting but the chapter “Form Generation” is too succinct (it’s a pity because I think it is one of the rare texts dealing with the subject).
* About systematic design, the famous Engineering Design, A Systematic Approach (Book) by Pahl&Beitz. Very interesting also, deals a little with preliminary design (steps briefly described, some rules, principles and guidelines) but there is not in my opinion a detailed procedure/methodology for preliminary design phase.
* Mechanical Design of Machine Elements and Machines: A Failure Prevention Perspective (Book) by Jack A. Collins. It has a chapter “Basic Principles And Guidelines For Creating Shape And Size” (you can read it partially with Google Books: (link towards the correct chapter). It seems to be an interesting list of advices but still no methodology.
Thank you in advance.
PS: I have created the same thread in “Optistruct” forum section (Link) as my questions are related to both Optistruct and Inspire.
Best Regards,
Florent
Answers
-
Hi @florentb
Let us consider a small example on how select a design and non-design space for a topology optimization.
Consider you are assigned to design a See-Saw as shown in the image below:
<?xml version="1.0" encoding="UTF-8"?>
Now write down the design conditions for non-design regions: 1) It should have enough space to accommodate 1 child on both sides with an area of 50*50cms. So make 50*50cm on each side as your non-design space
2) Next condition is the base should be a fixed support. So you can't take material OFF from the base. So this will be your non-design space
3) See-Saw should swing around an axis at a point/area and this should be equi distant from either edges. So make this as your non-design space
This is how you have to consider design and non-design space based on the requirement and how it design should operate in a working condition.
Note: These are few ways to select design and non-design ways based on practical experience.
0 -
Dear Prakash Pagadala,
Thanks for your answer.
I realize maybe using the expression 'design space' in my question was a bit confusing. Actually I am not asking how to select design and non-design spaces. I have a good understanding of that part of the process. For example, putting non-design space around functional surfaces and interfaces like holes, etc...
To be more exact, I am looking for a 'methodology' (or method, process, procedure, rules or guidelines) to determine a preliminary rough geometry to a mechanical part inside a mechanical system from a set of requirements. So I can use that rough geometry as my model on which i will define 'design space'+'non-design space'.
Maybe my question will be much clearer if I use some examples:
* Let's say you want to design a structural part for an Internal Combustion Engine. You can first determine an envelope (the maximum space/volume) of the part you are designing. One possible methodology would be to start with a large volume from which you will subtract the volume of all surrounding components.
* Another example: You want to design a car structure. One possible methodology for example to determine the envelope of the structure you are going to optimize is to start from the styling envelope (the exterior volume of the car) and then subtract the volume of each component of the car and other volumes (like volume for occupants, volume for the trunk, etc) from the styling envelope. Once you have obtained that 'structure envelope' you will still have to define design and non-design space to keep interfaces, attachment points, etc...
In the previous examples I gave, you see you already have a lot of information (volume of the system, volume of components, etc) available for your design, you can easily create a model and then select design and non-design space.
If I go a bit further, let's say I want to design an innovative mechanism with some different and non-standard components/bodies. I would start the preliminary design process by defining the topology of the mechanism. For that, I will maybe draw a kinematic diagram (also called kinematic scheme or skeleton diagram). But the next step is to give a preliminary rough shape to each body (embodiment design) so I can then use topology optimization to find an optimal 'final' geometry. 'Finding a preliminary rough shape' is not so obvious for me. I think the shape has to be chosen carefully to avoid missing some good alternative structural concepts.
The only methodology is see at the moment is the old 'trial and error' but I am looking for a more systematic methodology.
I am aware that my question goes far beyond simply using Optistruct/Inspire and it is more a methodological question. As I said in my initial question, I think it actually deals mainly with configuration design (arrangement of the individual components, determination of interfaces, space allocation, etc.). By the way, as I think some of you are experienced mechanical engineers maybe you will be able to give me some advices or some lines of thought.
Sorry for my imperfect English.
Thank you.
Kind Regards,
Florent
0 -
Hi Florent,
We would advice you to use the maximum possible volume or space, this is the best approach before topology optimization.
0